世の中は次第にデジタル化されており、生産性の高いハイテク工場のDXの導入率は非常に高くなっています。 一方で中小企業の工程管理でよく耳にすることが「デ…
はじめに
目次
“「現場帳票研究所」”に寄稿させていただくことになりました株式会社K-crew代表取締役の北川といいます。
この連載は、現場DXに取り組むチームリーダー、またはITツールを活用した改善提案に携わる方に向けたものです。
著者の北川が経験してきた生産現場の業務改善事例や現場のお困りごとをもとに、DX推進の気づき・ヒントをお届けして参ります。
この記事を読むと以下のメリットがあります。
1.現場改善の基本となる考え方がわかる
2.ITツールに飛びつかない現場改善手法がわかる
3.業務目的の本質を見抜くことの重要性がわかる
「現場改善は、課題の本質に気づく能力にかかっている」
第一回は、「現場改善は課題の本質に気づく能力にかかっている」というテーマで話をします。
現場課題に気づける人間が1人いたとしても、その課題と解決案を現場担当者に伝えるだけでは中々、会社全体の改善活動には繋がらないことがほとんどです。
どうすれば部署単位や会社全体を巻き込んだムーブメントになるのか?
ルールを変えるのは、「大変」?
便利なITツールを使っても使わなくても、業務改善による効率化を図るのは可能です。
業務改善とは業務が「善い方向」に「改め」られれば良いわけですが、現場のみなさんは結構悩まれています。
“業務の品質を落とさず、短い時間で同じこと(或いは品質を上げる)”を実行すれば良いだけなのですが、いろんなことを考えすぎてしまう様です。
これはお客さんの所で経験した事例なんですが、どこの会社でも同じ様な事が起こっているのではないでしょうか?
業務を簡単に説明しますので、どこが問題でどう解決してきたかを一緒に考えていきましょう。
【生産情報の伝達】
① 生産管理課のAさんが今月生産する計画を立てて、工程表を作成しそれぞれの現場に配布する。
② 工程表を受取った製造課のB係長は計画通りに生産できるかを確認する。そして問題なければ製造事務所(休憩所も併設しているので所属する部下との情報共有スペース)のホワイトボードの工程表に生産計画を記入し、係内の生産計画を共有する。
③ 係に所属するC作業長は管理室の工程表を見て、自分の担当する製品の工程を確認する。
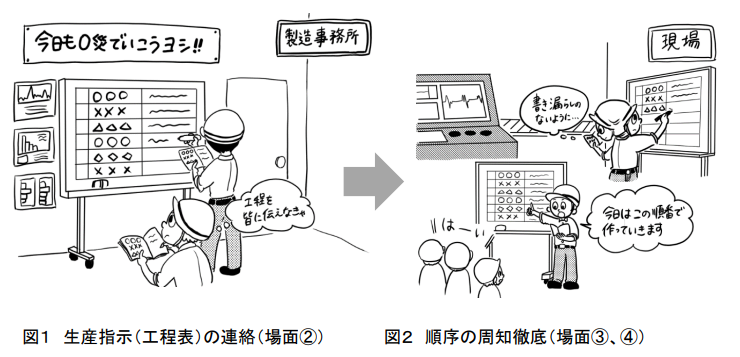
④ 作業長C(ヒエラルキーの上位から、課長―係長B―作業長C―作業者モブです)は現場作業者や作業補助の人達にも情報を共有してもらうために、管理室の工程表をメモして、現場作業場の近くにあるホワイトボードに工程を書き込む。
⑤ これで当日或いは今週の生産品目を皆と共有出来るようになったので、生産や生産品目の切り替えがスムーズになります。
というような風景が普通にあります(日本の製造現場は超真面目なのです)。
20年くらい遡れば、この様な状況が本当に普通の風景でした。
さて、ここで問題です。
i-Reporterのような便利なITツールがない時代に、末端の作業者まで生産計画周知徹底する方法を考えてみてください(20年くらい前ならどんな改善をするかです)。
昔から普通に使っているコピー機やFAXなどは使っても良いです。
【一つの答え】
改善の方法はいろいろあるので、これが正解というわけではありません。
登場人物は、工程表を作成したAさん、工程表を受け取ったB係長、B係長からの情報を生産現場と共有しようとするC作業長、あとその他大勢の現場作業者です。
それぞれの担当者は、“受け取った情報”は伝達すべき情報なので、どんどん次工程に渡していくという作業を繰り返していきます。
この作業は、受け取った情報(の一部)の形を変えて伝達しているだけです(昔はこの方法が主流でした)。
この作業の目的は、製造課全体に重要な情報を共有し周知徹底することです。
“前工程で受取った自分は、その情報を次工程に渡す“という前後工程だけを忠実に実行すれば目的は達成できます。
でもこのような伝言ゲームで本当に良いのか?もっと良いやり方があるのでは?と考えます。
ちゃんとした情報を愚直に伝達することはゲームとしては全然面白くありませんが、この伝言ゲームを最速にするためには、どうすれば良いか?
答えは簡単です!
最初の人が最後の人に答(情報)を伝えれば最速に情報を伝えることが出来ます。
“伝言ゲーム“としては、全然面白くありませんがね。
では、工程表の問題に置き変えればどうなるかというと以下の様になります。
最初に貰う“工程表”は通常A4とかA3のサイズになるでしょうが、A0に拡大コピーしたものを2枚もらって、管理室と現場の作業場に貼れば済むことです。
現在であれば、そのエクセルファイルを現場の大型モニターに写せばよいだけですけど、今回は制約で使えません。
ここで重要なのは、“伝言ゲーム”をやっていた人達が自らこの“無駄”に気付いて改善しないといけないと思うことです。
便利な道具で解決手段を簡単に与えるのではなく、“本当の課題”に皆が気付いて現場だけでなくいろんな部署から改善の声が上げるような組織にするという事が非常に重要なことです。
この様な“課題解決の声を上げる”の場が作れれば8割くらい改善は成功したようなものです。
いろんなやり方があると思いますが、みなさん(の会社)はどの様に、この様な課題を解決していきますか?
次回は、それでも簡単に変えられない“しがらみ“の様なものについて話したいと思います。
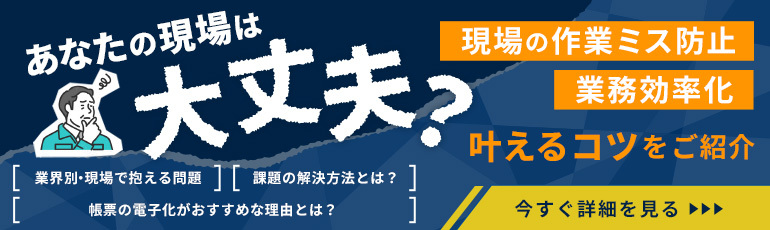
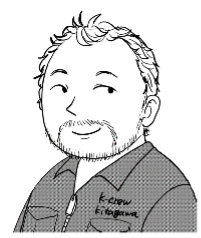
株式会社K-crew 代表
(http://k-crew.com/)
1990年に積水化学工業京都研究所に入社。
流動解析ソフト開発や住宅資材・管材製品の開発に従事した後、工場に転勤。
開発した製品群の受注から生産、出荷までの業務改革プロジェクトを推進を担当。
デジタル化の重要性を認識し、2Dから3Dへの設計業務改革及び、
CAD等のツールを活用した製品開発・生産プロセスの改革に取り組む。
その後、積水化学を退社し、現在は、設計業務の2Dから3Dへの移行を支援する会社を設立。
i-Reporterを用いて、品質データのデジタル化を推進し、製造業を中心に業務改善に注力。
また、飲食店の効率改善指導や食品会社の生産性向上も実施。
製造現場のデジタル化を推進し、業務プロセスの改革を客と共に行うとともに、
システム化による改革を推進してきました。
最近では、センサー、画像処理、形状計測、サーマルカメラ等から直接品質データをリアルタイムで取得し、
ビッグデータ分析に用いて生産性向上に取り組んでいます。