目次
製造現場においてもっとも気を付けるべきことは、作業者による事故の防止です。
多くの事故は突発的なものではなく、「ヒヤリハット」と呼ばれる危険の兆候を見逃した結果として発生します。
事故を防止するには、日頃から「ヒヤリハット」に対する意識を高め、対策しておくことが重要です。
今回は、製造業における事故防止のためのヒヤリハット活動について、具体的な事例と対策を解説します。
ヒヤリハットとは
まず、ヒヤリハット活動の概要や主な原因について見てみましょう。
ヒヤリハットとは?
例えば、工場を歩いているときにフォークリフトが死角から出てきて「ヒヤリ」としたり、棚に保管していた重い荷物が落ちかけて「ハッ」としたりするケースが挙げられます。いずれも製造現場などではよく見られるケースです。
「ヒヤリハット」は日本語をもとに作られた言葉ですが、海外では「ハインリッヒの法則」として知られています。
ハインリッヒの法則とは、1931年に米国の損害保険会社で働いていたハインリッヒ氏が労働災害を調査した結果から得た法則のことです。
ハインリッヒ氏の調査によると、1件の重大事故が発生した場合には、29件の軽微な事故と300件のヒヤリハットがその背後に隠れているとされています。
つまり、危険な状況や軽微な事故を見過ごし続けた結果として、重大な事故が起こってしまうのです。
ハインリッヒ氏の調査に基づき、1件の事故を防止するためには300件のヒヤリハット対策が必要であるといわれています。
ヒヤリハットの起きる原因
ヒヤリハットの多くは人為的なミスによるものです。
ここでは、ヒヤリハットの主な原因となる人為的ミスのパターンを紹介します。
■焦りや油断
製造現場では、事前に決められた作業内容・時間に沿って業務を行います。
新しく配属された作業員は業務に不慣れなため、時間内に終わらせようと焦ってしまうでしょう。
また、一方で作業が慣れた頃には油断が生じてしまうものです。
焦りや油断は正確な判断や行動を妨げる要因となるため、ヒヤリハットにつながりやすいといえます。
■作業者の疲労
長時間作業を続けていれば、作業者に疲労がたまります。
また所定の勤務時間を守っていたとしても、作業内容によっては一部の作業者に過度な疲労がたまることもあるでしょう。
疲労がたまれば集中力が低下してミスが増えるため、ヒヤリハットも発生しやすくなります。
■5Sの不徹底
5Sとは「整理」「整頓」「清掃」「清潔」「しつけ」の頭文字をとった言葉です。
製造現場では、作業の基本として5Sの徹底が指導されます。
5Sが徹底されていない現場では用具・工具が所定の場所に保管されていなかったり、汚れによって床が滑りやすくなっていたりするなど、想定外の事象が起きやすくなります。
ヒヤリハットだけでなく、品質面の問題につながる可能性もあるでしょう。
現場帳票をデジタル化を使えば、アラート表示や通知で不良要因の発生時には即時関係者に連絡が可能です。
現場帳票システム「i-Reporter」を用いたリコール・クレームの解決事例をご紹介しています。
あなたもi-Reporterを使ってみませんか?
→資料ダウンロードはこちら
製造業におけるヒヤリハット事例
製造現場でよくあるヒヤリハット事例を3つ紹介します。
【ヒヤリハット事例①】歩行者とフォークリフトが接触しそうになる
工場や倉庫内では、フォークリフトなどの運搬用機械と人が接触するという事故がよく起こります。
通路を通るのは歩行者だけではないため、普段工場や倉庫に出入りしていない人物が作業場所に入る場合などは特に要注意です。
フォークリフトの運転者は、前方は荷物で見えにくいためバック走行を行います。
体をひねって後方を確認しながら走行しますが、常に視界を確保できているわけではありません。
歩行ルールが徹底されている状況に油断し、よく確認せずに走行する作業者もいるでしょう。
歩行者・フォークリフト運転者の双方が十分注意しなければ、接触事故のヒヤリハットが発生しかねません。
【ヒヤリハット事例②】機械に手や指を挟みそうになる
設備を使った加工作業などをする際、一度コンベアーに置いた加工品を再度触ろうとして手や指が巻き込まれるという事故もよくある事例です。
加工品の位置がずれたり、作業の漏れに気づいたりすると、つい手を出してしまうものです。
機械をストップすると全体に迷惑をかけるため、自力で処理しようという意識が働くこともあるでしょう。
【ヒヤリハット事例③】回転する器具に軍手や衣服が巻き込まれる
製造工程において、手や指を挟まないよう十分注意していても、軍手や衣服など身につけたものが巻き込まれるという事故が起こることもあります。
大きめの軍手や衣服を身につけている場合、気を付けているつもりでも少しはみ出た部分が機械に接触することは十分起こりえます。
事故防止のためには衣服のサイズ調整や、不要な場所では軍手を外すといったルール整備など、細かなケアが求められるでしょう。
【ヒヤリハット事例④】エンジン部品(ピストン)の組み立て時の位置指示が数mm誤って記載されていた
誤記載が原因でエンジン性能に影響を及ぼし、最終的には車両の大規模リコールに繋がりました。
その結果、企業の信頼性、販売、ブランドイメージに 大きな打撃を与えてしまいました。
記録精度と細部への注意力の重要性が明確になりました。
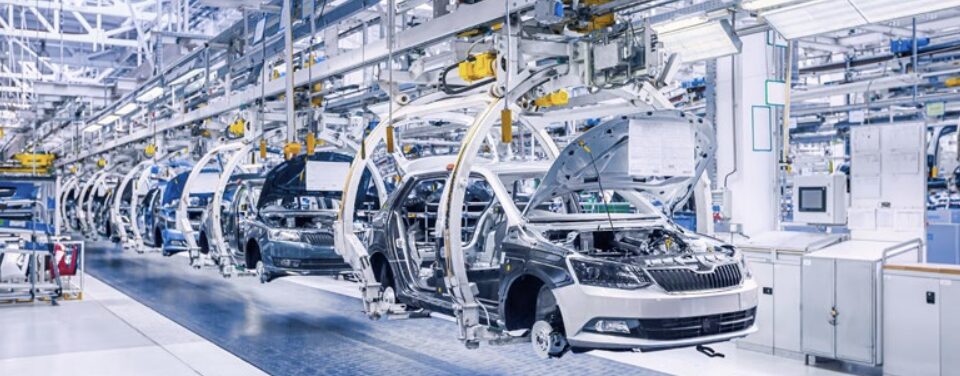
【ヒヤリハット事例⑤】アレルギー反応を引き起こす可能性のある小麦粉の使用量が誤って半分の量で記載されていた
包装に記載すべきアレルギー警告表示が欠け、誤った情報が記載された製品が市場に出荷されてしまいました。
消費者からのクレームで事故が発覚し、大量リコールにつながりました。
記録の正確性は製品の品質だけでなく、消費者の安全に直結するものだと改めて認識をすべきでしょう。

【ヒヤリハット事例⑥】トランスミッション部品の製造過程で、作業表が管理ミスにより保管されることなく誤って廃棄された
トランスミッション部品のギアに欠陥が発覚しましたが、作業表が存在しなかっ たため、ロットや製造時間帯の特定が困難になりました。
正確な記録とその保管の重要性が明らかになりました。
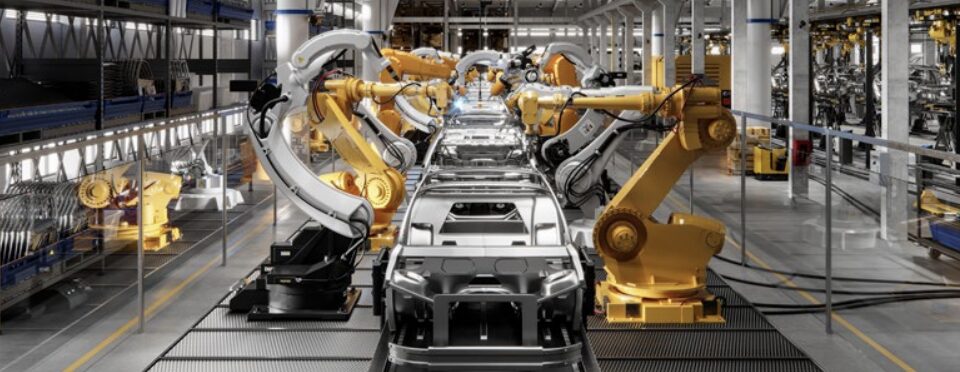
【ヒヤリハット事例⑦】製造現場で使用される作業表の一部が誤って廃棄された
特定の製品ロットに問題が発覚しましたが、製造日、ロット番号、使用された小麦や卵などの原材料情報といった製品追跡に必要な情報がなく、該当製品の特定とリコールが困難になりました。
記録の適切な保管と管理は、製品の品質管理や消費者の安全に直結するということを改めて認識することが求められます。
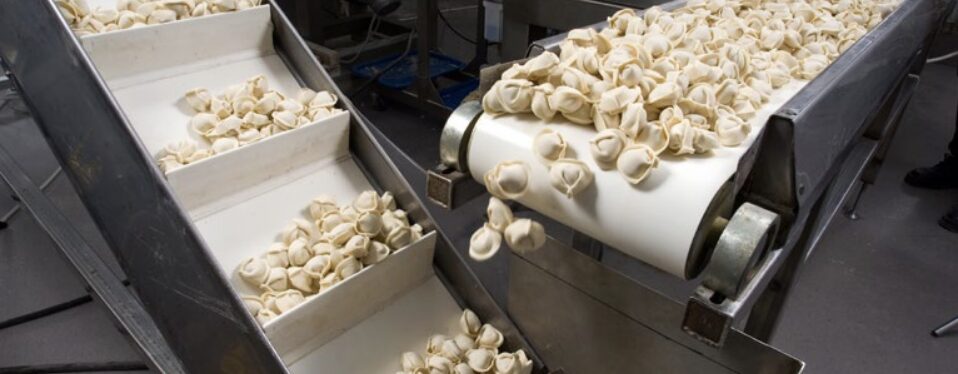
【ヒヤリハット事例⑧】製造ライン上でブレーキパッド部品に不良が判明したが、情報がタイムリーに品質保証部門に伝達されなかった
結果、数百セットの不良品が出荷され、顧客からのクレームやリコールを引き起こしました。
製品の品質保証には不良情報の速やかな報告・共有が重要です。
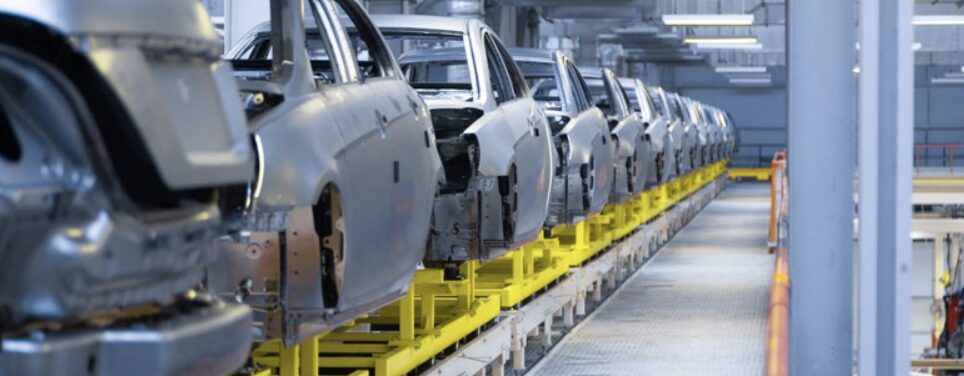
【ヒヤリハット事例⑨】製造ラインでチョコレートに原材料の混入が確認されたにもかかわらず、情報が適切に報告されなかった
該当ロットの商品が市場に出回り、製品のリコールとその対応に莫大なコス トと時間を要する事態へと発展してしまいました。
現場からの報告は迅速かつ正確でなければなりません。
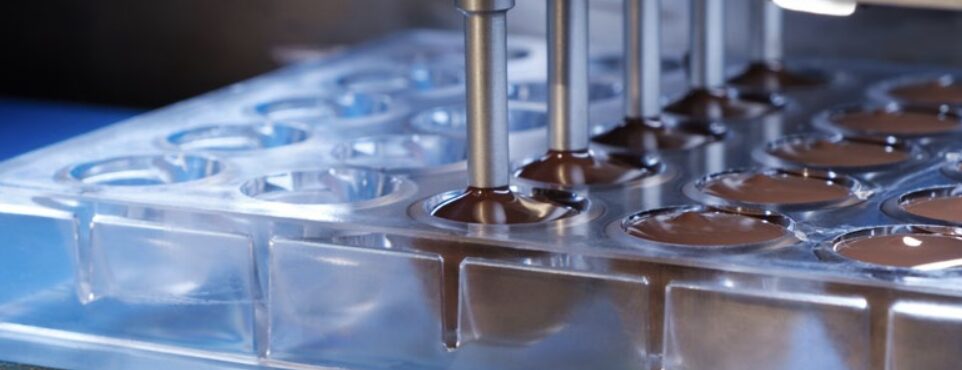
事故防止のために
紹介したヒヤリハット事例のほかにも、製造現場にはさまざまな事故のリスクが潜んでいます。
事故防止のために、ヒヤリハットを活用する方法について説明します。
【事故防止のために①】報告の習慣化
ヒヤリハットはあくまで「事故になりかねなかった」事例です。
そのため、その場限りのできごととして十分な報告がなされない可能性があります。
ヒヤリハットの重要性について現場でしっかりと共有し、報告を徹底するよう周知しましょう。
報告を習慣化できれば、一つひとつの原因を解消することで重大な事故の防止につなげられます。
報告されたヒヤリハット事例については、専用の報告書にまとめるなど記録体制も整えておきましょう。
【事故防止のために②】原因の分析
ヒヤリハットの報告を習慣化できたら、次に重要なのが原因分析です。
原因分析においては、ヒヤリハット発生当時の様子を細かく把握する必要があります。
あとで原因を分析できるよう、場所や時間などの5W1Hを報告書に記載するようルール化するとよいでしょう。
当人だけに任せた場合、思い込みや先入観によって事実と異なる記述がされる可能性もあります。
組織のメンバーや上司による確認を必須とするなど、客観的な事実に基づく原因分析ができる仕組みを整えましょう。
【事故防止のために③】再発防止策の周知徹底
ヒヤリハットの原因分析ができたら、再発防止策を検討します。
事例を共有するだけでなく、同様のヒヤリハットが二度と起きないよう万全を期す必要があります。
例えば、本記事でも紹介した歩行者とフォークリフトの接触であれば、フォークリフトがバック走行するエリアの歩行を禁止したり、フォークリフトと歩行者の移動エリアを分けたりするなどの対策が考えられます。
関係者間で事故防止の対策を協議し、決定しましょう。
決まった対策は、作業者全員に周知徹底されるよう定例会などで共有します。
ヒヤリハットを事故防止に活用するためには、発生したタイミングで迅速に報告できる仕組みが大切です。
報告が後回しになれば、5W1Hなどの情報があいまいになりやすいほか、危機意識も薄れてしまうでしょう。
事故の状況を5W1Hで詳しくまとめられるよう、標準のフォーマットを用意して作業者全員に共有するのがおすすめです。
さらに、ヒヤリハット報告書はデジタルデータにすることで効率的に管理できるでしょう。
デジタルデータであれば、原因分析や社内共有もスムーズに実施できます。
まとめ
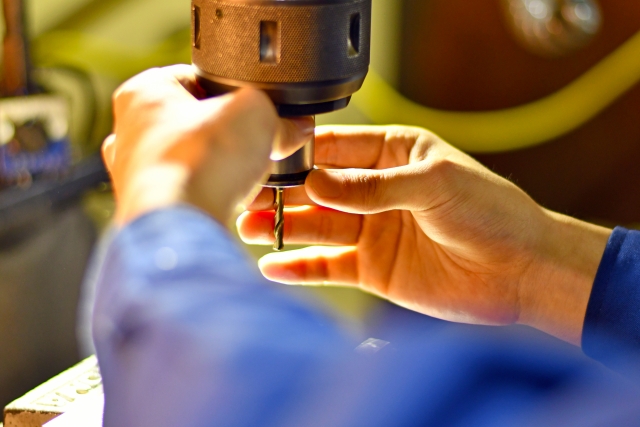
ヒヤリハット事例は、将来の事故を防止するための重要な情報です。
工場や倉庫におけるヒヤリハットを放置すれば、いずれ重大な事故につながってしまうかもしれません。
作業者からヒヤリハット報告があった場合は、たとえ作業者による過ちが原因だったとしても報告を上げたこと自体は評価すべきです。
報告がしやすい環境を作ってこそ、ヒヤリハット活動は効果を発揮します。
ヒヤリハット事例をもとに事故防止の仕組みを構築し、健全な事業運営につなげましょう。
健全な事業運用をするために、現場帳票をデジタル化しませんか?
特に現場帳票システム「i-Reporter」では以下のことを実現できます。
・報告書を電子保存して一括管理
・エクセルでダウンロード可能
・アラート通知で不良要因の発生を関係者に連絡
・報告書をリアルタイムで共有可能
あなたもi-Reporterを使ってみませんか?
→資料ダウンロードはこちら

現場帳票研究所の編集部です!
当ブログは現場帳票電子化ソリューション「i-Reporter」の開発・販売を行う株式会社シムトップスが運営しております。
現場DXの推進に奮闘する皆様のお役に立てるよう、業界情報を定期的に配信致しますので、ぜひ御覧ください!