目次
製造現場において、作業の効率化は絶えず求められる課題です。
しかし、効率化を実現するにあたり、どのような手段を取るべきか迷ってしまうケースも多いでしょう。
本記事では、高い生産性や品質管理を実現するための基盤となる「標準作業」の要点を解説します。
標準作業の策定に必要な3要素や3票についても詳しくお伝えしますので、作業効率の低下やリードタイムの長期化などの課題を抱えている企業様は、ぜひ参考にしてください。
標準作業の目的
作業手順を最適化し、業務を効率化するには、まず標準作業を定める必要があります。標準となる作業が決まっていなければ、現状のどこに問題があり、どこを改善すべきなのか判断できないためです。こちらでは、標準作業の概要や目的をご紹介します。
標準作業とは
標準作業とは、商品をより早く、安全に無駄なく製造するための作業方法のことです。
人の動き方を中心に、物や設備のもっとも効率の良い組み合わせを検討して実行します。標準作業を定めることで、担当者が作業手順や使用する道具を理解しやすくなり、迷うことなく作業を進められるメリットがあります。
標準作業の策定には、「3要素」と「3票」と呼ばれる現場改善のための手法を用いるのが一般的です。
3要素とは、「タイムタクト」「作業順序」「標準手持ち」の3つを指します。3票とは、「工程別能力表」「標準作業組み合わせ票」「標準作業票」の3種類の帳票のことです。それぞれの意味や役割、作成手順については後述します。
標準作業を行う目的
標準作業を定める主な目的は、製造方法とルールを明確化し、能率を向上させるためです。標準作業を構築することで、作業者の動き方を統一しやすくなり、生産性の向上が期待できます。また、作業方法や管理方法の違いによって生じる無駄も抑えられます。
このほかに、標準作業は作業が適切に行われているかの判断基準を作るためにも重要です。現在の作業が標準作業に達していないときは、どこかに問題があると考え、改善に努めることができます。
標準作業における3要素
続いては、標準作業における3要素の意味や役割について解説します。標準作業の3要素を決めることで、人の動きと物や設備の効率的な組み合わせを考えて無駄を減らすことが可能です。
タクトタイム
タクトタイムとは、製品や部品を1つ作るために必要な時間を意味します。製造業では、欠品や過剰在庫の防止を目的として、一定時間内に生産すべき製品の必要数を決めるのが基本です。それを達成するためには、各製品や部品の製造にどのくらいの時間をかけるべきかが重要になり、その時間をタクトタイムと呼びます。
タクトタイムは、「稼働時間÷必要生産数」の計算式で算出可能です。なお、タクトタイムの計算に余裕率は見込みません。余裕率とは、正味時間に対する余裕時間の割合のことです。タクトタイムは製品を1つ作る際の目標時間ともいえるため、余裕率を見込むことはありません。1サイクルの作業時間をタクトタイムに合わせていくことで、業務の改善につながり、可動率の向上が望めます。
作業順序
作業順序は、作業者が作業を効率的に行うための順序のことです。運搬や加工・組み立てなど、各作業の順序を効率面から見直すことで、製品の製造時間を短縮したり、作業の無駄を削減したりできます。
作業順序は、誰が作業しても効率よく行えるような流れになっていることが大切です。そのため、作業順序を最適化する際は、現場の作業員の意見を踏まえて実施するのが望ましいでしょ
標準手持ち
標準手持ちは、サイクルタイムと作業順序を守ったうえで、繰り返し作業を実行するために必要な最小限の仕掛品の数を表します。サイクルタイムは1つの工程に実際にかかる時間を意味し、仕掛品は工程内で作業中の未完成な製造品を指す言葉です。サイクルタイムには、機械に材料のセッティングをしたり、検査をしたりする時間も含みます。サイクルタイムは、「稼働時間÷実際の生産数」で計算可能です。
標準手持ちが多すぎると作りすぎが発生し、作業スペースの無駄な占有や後工程での作業ロスにつながるリスクがあります。反対に標準手持ちが少なすぎると、作業待ちが発生して生産性が低下します。そのため、標準手持ちは、ワークフローやレイアウトを考慮して適した数を設定することが大切です。
標準作業における3票
こちらでは、標準作業の構築に使用される3票の特徴や作成する目的、作成方法についてお伝えします。
3票を作成すると現場改善や管理、指導をスムーズに行いやすくなります。
工程別能力表
作成する目的
工程別能力表は、各工程の生産能力を把握する目的で作成される帳票です。各工程にかかる手作業時間や自動送り時間などを記入することで、ライン全体の加工能力やボトルネックとなっているネック工程を明らかにできます。ボトルネックとは、全体の作業工程の中でもっとも良くない影響を与えてしまっている箇所を意味する言葉です。
工程別能力表は、改善のターゲットや優先順位を決める際にも役立ちます。工程別能力表を使って各工程の生産能力を比較することで、どの工程に問題があるのか、どの工程を優先的に改善すべきかなどの点を速やかに判断できるためです。また、工程別能力表は、後述する標準作業組み合わせ票を作成する際の資料にもなります。
工程別能力表の一般的な作成方法
①工程能力表を作成する際は、まず製品の基本情報となる品番、型番、品名、個数などを記入します。
これにより、どの製品に関する生産能力を確認しているのかを明確にしましょう。
②各工程の順番や工程名称、機番を記載します。工程ごとの情報を明確にすることで、製造の流れを視覚的に理解しやすくなります。
③基本時間欄に手作業時間と自動送り時間を記入しましょう。
手作業時間は、作業員が実際に手を動かして作業を行う時間のことです。工程間を移動する際の歩行時間は含みません。
自動送り時間は、設備を起動してから作業が完了して停止するまでの時間を指します。
④刃具欄に刃具交換個数と交換時間を記載しましょう。
製造過程では多くの刃具が使用され、その交換にも一定の時間を要します。そのため、各工程の生産能力を比較するには、工程ごとに使用する刃具の個数と交換時間を事前に確認しておく必要があります。
⑤上記の情報を参考に各工程の加工能力を計算し、数値が一番低い工程をネック工程として記録しましょう。
加工能力は、「稼働時間÷(製品1個あたりの完成時間(手作業時間+自動送り時間)+製品1個あたりの刃具交換時間(刃具交換個数÷交換時間))」で計算可能です。
業務改善を進める際は、ネック工程から優先的に着手することになります。
また、備考欄に手作業と自動送りの線図を記載すると、ネック工程の可視化に役立ちます。手作業時間は実線、自動送り時間は点線など、線の種類を分けて記入するとわかりやすいでしょう。
標準作業組み合わせ票
作成する目的
標準作業組み合わせ票は、作業者の動作における無駄を発見・改善するための帳票です。具体的には、1人の作業者が担当する作業範囲を洗い出したうえで、サイクルタイムとタクトタイムを比較します。もし両者に開きがある場合には、その差を埋めるための改善点を検討します。
標準作業組み合わせ票は、作業者1人につき1枚作成するのが基本です。作業者と設備の適した組み合わせや作業順序を見直すことで、サイクルタイムをタクトタイムに可能な限り近づけることを目指します。また、標準作業組み合わせ票は、後述する標準作業票を作成する際のベースにもなります。
標準作業組み合わせ票の作成方法の例
①標準作業組み合わせ票を作成する際は、まず時間軸にタクトタイムの時間を赤線で引きましょう。
作業者の目標となる線のため、視覚的にわかりやすくするのがポイントです。
②作業内容の欄にそれぞれの作業内容を記入し、実際の生産に沿った手作業も追加します。
具体的には、「材料を取る」「完成品を並べる」などの項目が考えられます。
そして、各作業にかかる時間を記入したら、時間軸にも線を引いてサイクルタイムを確認しましょう。
手作業時間は実線、歩行時間は点線など、線を使い分けるとわかりやすくなります。
③サイクルタイムとタクトタイムを比較し、開きがある場合は改善点を検討しましょう。
標準作業票
作成する目的
標準作業票は、作業工程全体を可視化し、改善点を検討するための帳票です。工程別能力表や標準作業組み合わせ票に基づき、具体的な作業者の動きや機械の配置、作業の手順を1枚の帳票にまとめることで、作業の全体像を把握しやすくします。また、標準作業の3要素(タイムタクト、作業順序、標準手持ち)を示すことで、歩行や手持ちなどの無駄、安全や品質のチェックなどのポイントを確認できます。
標準作業票の作成方法の例
①標準作業票を作成する際は、まず作業内容の欄に、標準作業組み合わせ票に記載した最初の作業と最後の作業を記入しましょう。
これにより、作業者の作業範囲を明確にします。
②作業現場のレイアウトに対応するイメージ図を作成し、標準作業組み合わせ票に記載された作業手順に従って番号を記入します。各作業は番号順に実線で結んでおき、最後の作業から最初の作業への戻りは破線で示しましょう。これにより、作業の全体的な流れを可視化できます。
③標準手待ちや品質チェック、安全注意の印を必要に応じて設備や工程の位置に記入したら完成です。動線が長くなっている箇所がある場合には設備のレイアウトを変更するなど、作業改善に活用しましょう。
標準作業によって期待できる効果
標準作業を構築することで、製造業の現場にどのような効果があるのでしょうか。こちらでは4つの視点でお伝えします。
品質管理の向上
標準作業の策定は、安定した品質の維持に役立ちます。作業手順やルールが明確になることで作業が標準化され、作業者ごとのスキルや経験によるばらつきを減らせるためです。作業ミスや不良品の発生を防ぎやすくなり、再作業や廃棄による無駄の削減も見込めるでしょう。
生産性の向上
標準作業の構築は、生産性の向上にも寄与します。製造プロセスを見直し、無駄な動きや手順を省いたり、ネック工程を改善したりすることで、効率的な作業方法を確立できるためです。また、タイムタクトや標準手持ちを設定することで、生産計画や工程バランスの最適化も図りやすくなります。
安全性の向上
標準作業の導入によって作業工程が統一されることで、担当者が間違った方法で作業を行うケースを減らせます。その結果、ケガや事故につながる危険な動きを防止でき、安全性が向上します。5S(整理、整頓、清掃、清潔、躾)活動と合わせて取り組むと、より高い効果を実感できるでしょう。
育成期間の短縮
標準作業には、新人教育や異動者の教育時間を短縮する効果もあります。標準作業を策定することで、仕事の進め方を明確にでき、新人や異動者でもスムーズに作業内容を理解できるためです。育成期間を短縮して人材の早期戦力化を実現できれば、生産性の向上にもつながります。
標準作業に取り組む手順
最後に、標準作業を策定する際の手順とコツを6つのステップに分けて解説します。自社の製造ラインに課題を抱えている場合は、以下の手順で改善に着手してみましょう。
Step.1目的と前提条件を明確にする
まずは、標準作業を導入する際の前提条件や目標を具体的に設定しましょう。前提条件では、対象となる業務や範囲、使用対象者や管理者を決定します。目的については、生産効率の向上や品質の改善など、何を達成するために標準作業を導入するのかを明確にします。そして、標準作業の評価指数や目標値を設定し、達成度を測定できるようにしましょう。
Step.2作業内容を整理する
次に、実際の作業内容を整理して標準作業の3要素を算出し、3票を作成しましょう。現在の作業状況を観察し、無駄な作業やばらつき、手順の不備などがないかをチェックするステップです。
Step.3作業訓練を繰り返す
続いては、標準作業を設定し、作業者にその内容を伝えたうえで繰り返し訓練を行います。作業者が新しい作業手順や方法を理解し、規定通りに作業できるようになるまで、フィードバックや指導を継続するのがポイントです。
Step.4問題点を見つける
次のステップでは、標準作業を現場に導入し、現実とのギャップを確認します。作業訓練では見えてこなかった問題点や無駄がある場合には、5W1H(誰が、いつ、どこで、何を、なぜ、どのように)を用いて詳しく分析し、根本原因を特定しましょう。
Step.5改善提案をする
問題点や根本原因が特定できたら、次に、その改善策を検討します。改善策はPDCAサイクルで実施して、効果の測定や検証を行いましょう。PDCAは「計画・実行・評価・改善」の意味です。
Step.6新たな標準作業を作成する
最後に、上記の改善策が効果的であれば、新たな標準作業として現場に定着させます。標準作業の3票や標準作業手順書(SOP)を新たに作成して運用すると良いでしょう。目標達成に至らなかった場合は、ステップ4からの手順を繰り返すことで、標準作業をさらに最適化できます。
標準作業を策定して現場改善を実現しよう!
今回は、標準作業を定める目的や3要素と3票の概要、取り組みの効果、手順などをお伝えしました。
標準作業は、製造現場の効率化や品質向上を実現するために欠かせない考え方です。
作業の属人化や手順の不備により、生産性の低下やリードタイムの長期化が生じている場合は、標準作業を策定して現場改善を進めましょう。
製造現場で使用する書類の管理には、現場帳票システムの「i-Reporter」の活用がおすすめです。
【小売業界の作業精度と生産性向上へ】
現場帳票電子化ソリューション「i-Reporter」で店舗の業務をスムーズに!
・各店舗の在庫や売場の情報もリアルタイムで確認可能
・帳票を紙から電子化→報告のラグ削減、転記ミスの減少
・生産管理、点検、巡回、在庫管理を一括デジタル化
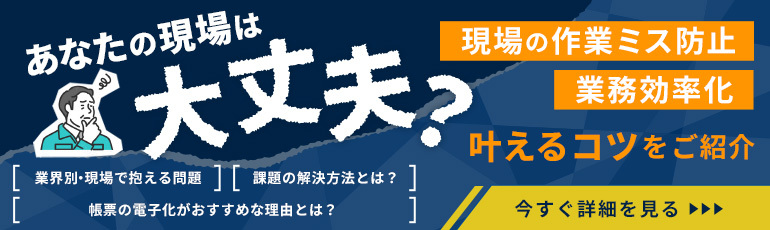

現場帳票研究所の編集部です!
当ブログは現場帳票電子化ソリューション「i-Reporter」の開発・販売を行う株式会社シムトップスが運営しております。
現場DXの推進に奮闘する皆様のお役に立てるよう、業界情報を定期的に配信致しますので、ぜひ御覧ください!