目次
製造業は、日本社会を支える重要な産業の1つです。しかし、労働生産性や国際競争力の低下、少子高齢化による人材不足など多くの問題を抱えています。
これらの課題を解決するために必要となるのが、業務効率化や品質向上に向けた取り組みです。
今回は、製造業における品質向上の重要性や施策の具体例について解説します。
ITソリューションを活用して品質向上や改善に成功した企業様の事例もご紹介しますので、ぜひ参考にしてください。
製造業における品質向上の重要性・メリット
製造業において事業を存続・成長させるためには、業務品質向上が欠かせません。製造品質の安定や向上は、顧客満足度の向上や信頼の醸成に直結し、最終的には売上アップにつながるためです。
反対に製品や作業の品質が低かったり、不安定な状態が続いたりすると、顧客からの信頼が低下し継続的な取引が難しくなってしまいます。
そのため、製造現場では常に自社の作業品質をチェックし、業務効率化や業務改善が可能なポイントがないか確認することが重要です。
<製造業の品質向上で予防できる問題・課題の例>
- 納期の遅れ
- 過剰在庫の発生
- 不良品の発生
- 計画外作業の発生
- クレームの発生
- 顧客からの評判・信頼の低下
- 新規顧客獲得の停滞
- ヒューマンエラーの発生
製造現場における品質向上には、工程管理・品質検証・品質改善の3つの要素が影響します。
工程管理=製造プロセスにおける作業員や設備のパフォーマンス、作業手順などを管理する業務。 業務標準化による属人化の防止や生産性の向上を目的として実施されます。
品質検証=完成した製品や自社の生産工程に不備がないか検査するステップ。 一定の基準に沿って検査を行うことで不良品や不適合品が出荷されるのを防ぎ、製品の品質を保証する役割があります。
品質改善=不良品が発生した場合に再発防止策を検討する業務。 不良品の発生要因を調査し、改善活動に取り組みます。 設計品質の改善や生産現場のムダの洗い出しなどを行い、将来における不良品の発生を未然に防止するのも品質改善の一環です。
上記3つの要素を総称して品質管理(QC)と呼ぶ場合もあります。
製造業における品質管理については、下記の記事で詳しく解説していますのでぜひご確認ください。
【工場の品質管理は何をする?仕事の種類や必要な考え方・手法】
製造業の品質向上につながる効果的な方法
製造業で品質向上を実現するには、自社の現状を可視化・定量化したうえで改善施策を検討し、組織全体で取り組むことが重要です。
この考え方を「総合的品質管理(TQM)」と呼びます。こちらでは、製造業の品質向上に役立つ具体的な施策をご紹介します。
5Sを徹底できる仕組みや環境をつくる
5S=整理・整頓・清掃・清潔・躾(しつけ)のこと。 Sから始まる5つの言葉をまとめて5Sと呼びます。
5Sは、品質管理における工程管理に用いられる手法・考え方の1つです。5つの徹底により職場の環境改善を図るための取り組みを5S活動と呼びます。
<5Sを徹底するための取り組みの例>
5Sを実施する場所 | 取り組みの具体例 |
工場・倉庫 | ・持ち出す道具の保管場所に「使用中」のプレートを置く ・作業が終わったら持ち場を清掃してから離れる ・作業手順や利用頻度を踏まえて工具の保管場所を最適化する |
事務所 | ・作業マニュアルや図面をデータ化して管理する ・整理整頓や清掃に関するルールを決めて従業員に共有する ・古くなった資料や伝票などは処分する |
4Mの分析で原因の特定・課題の選定をする
4Mとは、製造業において管理すべき4つ項目のことです。具体的には、人(Man)・機械(Machine)・材料(Material)・方法(Method)を指します。
4Mの管理を徹底することで、不良品が発生した場合の原因の特定や自社の製造プロセスにおける課題の把握が容易になり、品質向上に役立ちます。
人(Man)
4つの要素の中で特に重要とされるのが人です。製造業における品質を維持・向上するには、作業者のスキルアップが欠かせません。作業員一人ひとりの能力を把握したうえで、熟練度が低い場合には研修を実施したり、必要に応じて配置を見直したりする必要があります。
機械(Machine)
製造現場において効率的に製品を生産するには、機械や設備の稼働が不可欠です。
しかし、導入した機械に不具合や故障が発生してしまうと、製品の安定供給が難しくなります。そのような事態を防ぐためにも、機械の定期的なメンテナンスや点検、最新設備の導入などを行いましょう。
材料(Material)
製造業の品質管理では、製造に使用する材料にも注目します。材料の品質や量、調達手段を管理することで、不良品の発生防止やコスト削減を実現できます。
方法(Method)
製造業の品質向上には、作業方法の管理も欠かせません。
質の高い製品を安定して生産するには、各工程の作業手順や方法が標準化されている必要があります。作業手順書の作成やマニュアルの見直しなどが有効です。
DX推進により品質管理の改善を図る
製造業で品質向上を実現するには、DXを推進して品質管理の体制そのものを変革する方法も効果的です。
DXとは、「デジタルトランスフォーメーション(Digital Transformation)」の略称で、デジタル技術の活用でビジネスを改革する取り組みを指します。
製造現場におけるDXの例としては、まずIoT化による工場の見える化が挙げられます。
ITツールやAIを活用して工場内のあらゆる情報をリアルタイムで把握・分析できるようにすることで、品質の安定化や生産効率の改善、事故の防止につながります。
そのほかには、製造品質の向上に役立つシステムの導入も有効なDX施策です。
例えば、帳票管理システムや生産管理システムを導入すれば、人力で管理していた伝票情報や生産計画をすべてシステム上に集約できるようになり、現場改善が期待できます。
次のセクションでは、帳票管理システムを導入して品質向上を実現した企業様の事例をご紹介しています。
紙媒体やExcelによる管理工数の増大にお悩みの場合は、ぜひ参考にしてください。
製造業における品質向上の事例
製造業の品質向上には、現場帳票の電子化・ペーパーレス化ソリューションである「i-Reporter」の導入がおすすめです。
こちらでは、i-Reporterを活用して製造品質の向上を実行した企業様の事例を2つご紹介します。
日報の電子化で毎日1時間以上の作業時間を削減
最初は、ドキュメントソリューションの組み立てやトナーなどの消耗品の製造を行う、富士フィルムマニュファクチュアリング株式会社様の事例です。
こちらの企業では、製造現場における紙ベースの作業日報の管理に課題を抱えていました。
以前は各作業員が作成した作業日報を管理者が集め、エクセルへ転記する形で運用。手間と時間がかかるだけでなく、エクセルへの入力を待たないとデータを分析できないため、リアルタイムで現場の問題を把握できず、業務改善に遅れが生じていました。
そこで導入されたのがi-Reporterです。i-Reporterの導入後は、作業日報をタブレット上で作成できるシステムを構築しました。
日報の回収とデータ入力という、毎日1時間以上かかっていた作業がゼロになり、タブレットに入力された情報がリアルタイムで共有されるようになりました。
すでに導入済みの社内システムとi-Reporterを連携させることで、不良の発生を検知して即座に原因を追及する仕組みを実現し、現場の品質向上に役立てられています。
こちらの事例の詳細は、下記のページよりご確認ください。
【i-Reporterユーザー事例】日報を記入した紙の回収とデータ入力に、ラインリーダーが毎日80分もかけていたところ、その時間が「ゼロ」になりました
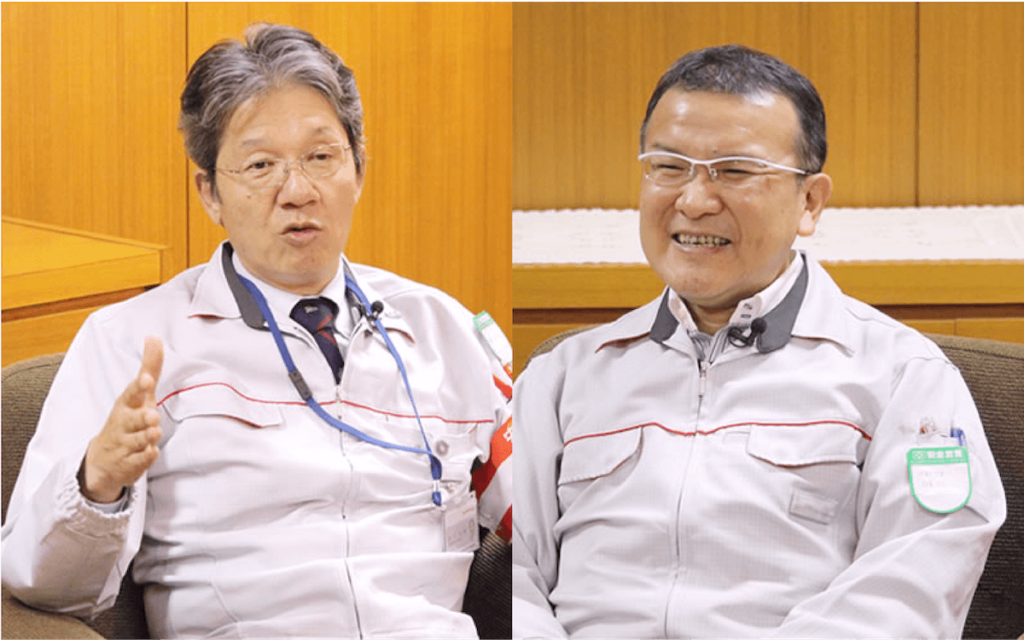
製造日報の電子化で月間170時間の時短に成功
続いては、プラスチック製品の製造・販売を手がける積水成型工業株式会社様の事例です。
こちらの企業では、製造日報の作成や管理、データ化の作業に課題を抱えていました。従来の仕組みでは各作業員が手書きで日報を作成。
担当者が集計したうえでデータ化しており、日報をまとめるためだけに残業が発生していた状態でした。
そこで同社では、i-Reporterを導入して製造日報の電子化に着手しました。タブレット上で日報を作成できるようにしたうえで、データが自動的に生産管理システムへ転送される仕組みを構築しています。Excelファイルも自動生成されるため、人力での集計や転記などの作業が必要なくなりました。
i-Reporterの導入後は、月あたり170時間の時短に成功し、残業時間の削減を実現しています。
また、同社の取り組みは積水化学グループ内の業務改善コンテストで銀賞を受賞しており、社内でも高く評価されています。
こちらの事例についてより詳細に知りたい場合は、こちらのページよりご覧ください。
【i-Reporterユーザー事例】i-Reporterを使って製造日報を電子化
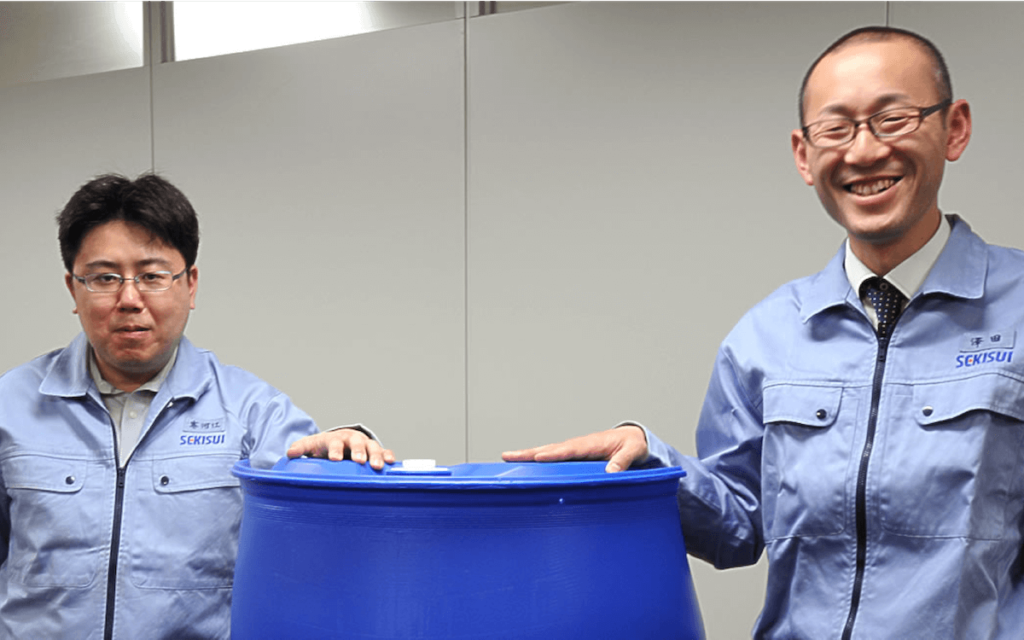
製造業の品質向上に取り組んで企業成長を加速させよう
今回は、製造業における品質向上の重要性や効果的な方法、帳票管理システムを活用した成功事例についてお伝えしました。製造現場の品質向上は、顧客の満足度や信頼に直結する重要な取り組みです。システムの導入や5Sの徹底、4Mの管理を通して品質向上を実現し、企業成長をさらに加速させましょう。
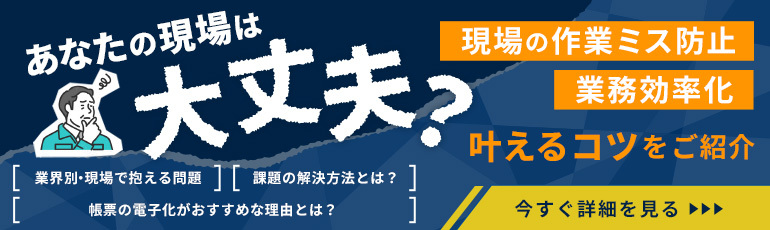

現場帳票研究所の編集部です!
当ブログは現場帳票電子化ソリューション「i-Reporter」の開発・販売を行う株式会社シムトップスが運営しております。
現場DXの推進に奮闘する皆様のお役に立てるよう、業界情報を定期的に配信致しますので、ぜひ御覧ください!