目次
サイクルタイムは、製造現場の生産能力を示す重要な指標です。サイクルタイムの短縮を実現することで、生産性向上や顧客満足度アップなど、さまざまな恩恵が得られます。
この記事ではサイクルタイムについて、リードタイムとの違いや時間の短縮方法を含めて解説します。製造業に携わる方や物流業界で仕事をしている方はぜひ参考にしてください。
サイクルタイムとは?
まずはサイクルタイムの意味やタクトタイム・リードタイムとの違いといった基礎知識を解説します。サイクルタイムに関する基本的な理解を身につけましょう。
サイクルタイムとはなにか
サイクルタイムとは、1つの製品が製造工程を開始してから完成するまでにかかった実際の時間のことです。加工時間だけでなく、待機時間や検査時間なども含まれます。
サイクルタイムを算出する計算式は、「稼働時間÷生産した製品の数=サイクルタイム」です。一般的な測定方法は、ストップウォッチを用いてサイクルタイムを測る方式がよく用いられます。
タクトタイムとの違い
タクトタイムとサイクルタイムには「予定の時間」と「実際の時間」という違いがあります。
タクトタイムは一つの製品を製造するのに必要な時間の目安です。製造の間隔を示すことから「ピッチタイム」とも呼ばれます。タクトタイムの計算式は「稼働時間÷生産必要数=タクトタイム」を用います。必要生産数とは、顧客からの生産依頼に基づいて決めた生産数のことです。
タクトタイムとサイクルタイムの関係性は、いわば理想と現実です。計算上の理想的な概念であるタクトタイムに、実際の生産時間であるサイクルタイムをなるべく近づけるよう努力することが重要になります。タクトタイムに対してサイクルタイムが長すぎる場合、納期に間に合わず、納期遅延や欠品を出してしまう恐れがあります。反対にタクトタイムよりサイクルタイムが短い場合、目標を上回って生産が完了できていることを意味しますが、過剰在庫の懸念があるため早すぎるのも問題です。
ちなみにタクトタイムは、理想的な最高効率の製造である「標準作業」を構成する3要素の一つです。標準作業の3要素にはほかに、「作業順序(最効率の手順)」と「標準手持ち(必要最小限の仕掛品)」があります。
リードタイムとの違い
サイクルタイムとリードタイムは「測定する工程の範囲」が違います。
リードタイムは、製品の発注から納品までにかかる実際の時間のことです。生産にかかる工程を測定するサイクルタイムと異なり、リードタイムでは商品の検品や出荷、配送などの時間も対象となります。
またリードタイムでは、工程間の待ち時間や仕掛在庫なども計測の対象とします。そのため、リードタイム短縮には生産スピードを速めることはもちろん、工程前後のムダの削減にも取り組むことが必要です。
サイクルタイムを短縮する方法
サイクルタイムを短縮するには、以下のような方法が効果的です。
ボトルネックを改善する
ボトルネックとは、生産工程で流れの速度が低下している箇所を指します。瓶の首にあたる細い部分の水流が滞ることに由来し、ボトルネックと呼ばれています。ボトルネックの主な原因は、材料の調達不足や処理能力の低さ、トラブルが発生しやすさなどです。
ボトルネックを特定し、改善を図ることでサイクルタイムの短縮が可能です。具体的には、材料管理の見直し、従業員のスキルアップ、トラブルの原因追究などの課題解決がボトルネックの改善につながります。
なお、ボトルネックを把握する際は、生産ラインの中で作業時間の長い工程や稼働率の高い工程に注目するのが有効的でしょう。稼働率の高い工程がボトルネックになりうる理由は、せわしなく動いていることがほかの工程に作業スピードが追いついていない可能性が高いからです。
切削条件を見直す
切削条件を見直し、最適化することでもサイクルタイムの時間の短縮が図れます。
切削条件とは、工作機械に入力する「回転数」「送り量」「切り込み量」などの数値の条件のことです。回転数や送り速度の調整を行い、それぞれの製造工程に合った設定を再検討することで、生産効率が上がります。
ただし、切削条件の変更は品質にも影響を与えるため、注意しなければなりません。その意味で、切削以外の時間であるアイドルタイム(アイドリングタイム)のほうを削減することも重要です。具体的には、マシンの起動準備や材料・工具待ちの所要時間を短縮したり、故障や停電などのトラブル対策を講じたりといった対応が想定されます。
そのほか、以下のような取り組みもサイクルタイム短縮のために取りうる現場改善の方策です。複数の改善策を組み合わせて実行することで、サイクルタイム短縮効果の最大化が狙えます。
- 「5S」を徹底する:「整理・整頓・清掃・清潔・躾」によって製造現場をきれいに保ち、トラブルを予知保全する
- 作業者のスキルアップ:研修や教育によって作業者のスキル向上を図り、ヒューマンエラーを防止するとともに動作の効率性を上げる
- 機械導入による自動化:高性能の設備やAIなどによって生産能力を高めるとともに、人為的なミスを防止する
- 進捗状況の見える化:生産管理システムなどにより各工程の状態を可視化、データ収集・分析による効率化も実現する
サイクルタイムを短縮できたときに得られるメリット
サイクルタイムの短縮を達成すれば、主に以下のようなメリットが得られます。
顧客満足度の向上が期待できる
サイクルタイムの時間の短縮は、顧客の期待に応えやすくなり顧客満足度の向上につながります。顧客への迅速な納品が可能になるためです。できる限り早い納品や数量が多い納品などの要望にも応じやすくなります。
利益の向上につながる
サイクルタイムを短縮すると、短縮前の同じ稼働時間内により多くの製品を生産することが可能です。生産数が上がり、納品可能な数量が増えることで、売上の増加が期待できます。
サイクルタイム短縮の目的は単なる生産時間の縮減ではなく、生産性向上につなげてこそ意味があります。真に生産効率を上げるにはデータだけを見るのではなく、ときには現場目線で方法やプロセスに無理がないか検討することも重要です。
サイクルタイムの短縮を実現しよう!
サイクルタイムの短縮は、製造業者に顧客満足や利益率の向上などのメリットをもたらします。短縮の実現には、ボトルネックの改善や切削条件の見直し、アイドルタイムの削減などの対策が有効です。
またITツールを導入して業務効率化を図ることも、サイクルタイムの短縮に好影響をもたらします。例えば、現場帳票システム「i-Reporter」では、お手持ちのiPadやiPhoneで製造現場の在庫管理・倉庫業務をデジタル化できます。IoTの力で倉庫管理を効率化することで、サイクルタイム短縮にとりわけ重要といわれる出荷作業に伴う梱包の時間縮減に有効です。
そのほか、i-Reporterは現場の日報・報告書作成や保守・メンテ業務、施工管理なども効率化でき、総じてムダな動作の削減やヒューマンエラーの防止をサイクルタイム短縮につなげられます。気軽に導入できるITツールでサイクルタイム短縮を図りたい製造業者の方は、ぜひi-Reporterの活用をご検討ください。こちらのページからお問い合わせいただけます。
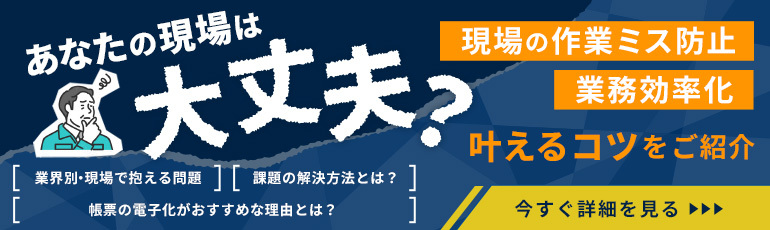

現場帳票研究所の編集部です!
当ブログは現場帳票電子化ソリューション「i-Reporter」の開発・販売を行う株式会社シムトップスが運営しております。
現場DXの推進に奮闘する皆様のお役に立てるよう、業界情報を定期的に配信致しますので、ぜひ御覧ください!