製造業をはじめとした幅広い業界や業種において、トレーサビリティの重要性がますます高まっています。トレーサビリティとは、製品や食品などがどのような経緯をたどって消費者の手に届くかを追跡できる仕組みです。
目次
企業にとって、トレーサビリティを確立することは、製品の品質向上や生産性向上だけではなく、消費者の信頼獲得にもつなげられます。
ここでは、トレーサビリティの基礎知識やメリット・デメリットから、トレーサビリティを向上させるポイントや導入時の改善例まで、わかりやすく解説します。
トレーサビリティとは
トレーサビリティとは、追跡という言葉の「トレース」と能力という言葉の「アビリティ」を組み合わせた造語です。
日本語では、「追跡可能性」と訳されます。
業界によって多少異なりますが、製造業では「原材料・部品の調達から加工、組立、流通、販売の各工程で製造者・仕入先・販売元などを記録し、履歴を追跡可能な状態にしておくこと」と定義されています。企業はトレーサビリティを確立することによって、安心・安全な製品を消費者へ提供しています。
トレーサビリティの種類
トレーサビリティには、次に挙げる2つの種類があります。ここでは、トレーサビリティの種類について説明します。
チェーントレーサビリティ
チェーントレーサビリティとは、製品がどのような流通過程を経由して消費者まで届いたのかを把握することです。
把握する必要があるのは、原材料から加工・組立、卸売・小売といった一連の流通過程の情報です。製品に問題が発生した場合、この流通過程を遡って調査を行います。チェーントレーサビリティは、自社だけでは成立せず、関係する全ての企業の協力が必要です。
関係する企業が1つでもトレーサビリティを怠ると、製品のトレーサビリティ全体に影響が及びます。そのためサプライチェーンの必要条件として、製品のトレーサビリティ管理体制が確立していることが重要になります。
内部トレーサビリティ
内部トレーサビリティとは、工場や倉庫ごとに記録する情報のことです。部品をいつどこから入荷し、いつ生産して検品結果がどうだったか、などを記録します。
内部トレーサビリティは、流通工程において重要な情報となります。また内部トレーサビリティを構築することで、品質向上や作業効率向上を図ることも可能です。
トレーサビリティのメリット
トレーサビリティを構築することで、様々なメリットがあります。
迅速に問題を追及できる
トレーサビリティを構築することで、製品に問題があった場合、迅速に対応することができます。
問題が発生した場合、まずはどこの工程の何が原因であったかを特定しますよね。
トレーサビリティを構築していれば、問題の特定が速やかに行えます。問題の特定が速やかに行えるということは、問題に対応する時間や手間などのコストを抑えることにつながります。
また、問題発生時の対応に必要なコストを削減できます。
製品の品質を向上できる
トレーサビリティは、製造工程だけに限らず、製品が消費者に届くまでの全ての流通過程を網羅する必要があります。そのため、問題が発生した時は責任の所在や原因の特定が明確になるため、対策を速やかに行えます。
自社の工程で問題を発生させないために、品質に関する意識が高まり、品質向上が図れるでしょう。
品質改善に必要な課題が明確になり、対応手段の確立と意識の改善が可能です。
顧客満足度を向上できる
自社製品を何度も購入する顧客は、製品自体に満足度を感じると同時に、製品がどのような流通経路で手元に届いたかを重視する人も多くいます。
似たような製品の場合、流通経路が明確な製品と、不明確な製品とではどちらを選ぶでしょうか。もちろん流通経路が明確な製品でしょう。トレーサビリティの構築は顧客満足度を高めることにもつながりますよ。
製造経路が明確になり、顧客満足度が向上します。
自社に対する信頼度が向上
たくさんの顧客が満足する製品を提供することは、企業の信頼度向上に必要不可欠ですよね。
そこで、顧客に対してどこで製造しているのか、どのような原材料を使用しているのかを開示することで、自社製品が安心・安全であることを証明できます。
トレーサビリティを確立することで、より企業の信頼度が上がることでしょう。外部から求められるトレーサビリティに対応することで、他社との差別化も図れます。
トレーサビリティのデメリット
さまざまなメリットのあるトレーサビリティですが、もちろん少なからずデメリットもあります。トレーサビリティを実現するためには、デメリットも理解しておきましょう。
コストがかかる
トレーサビリティシステムの導入と運用には、コストがかかります。
トレーサビリティシステムを導入するには、専用のソフトウェアやハードウェアの購入、システムの設備や機器の設置、データ管理のための人員などが必要となるため、初期費用が大きくなることがほとんどです。また、運用コストもかかり、管理システムの定期的なメンテナンスやアップデート、データの保存・管理にもコストがかかります。
コストをかけてトレーサビリティを導入しても、売上が増加するとは限りません。しかし、トレーサビリティを実施することで、消費者や取引先の製品に対する信頼性や透明性が向上し、その結果として売上の増加が期待できるでしょう。
従業員に負担がかかる
トレーサビリティシステムの運用には、新しい技術や手順を習得する必要があります。
新しい業務に慣れるまでの間、精神的に従業員へ負担がかかる場合があるでしょう。また、トレーサビリティのためのデータ入力や管理作業などが増えることで、日常業務における負担も増加する可能性があります。
作業工数が増える
トレーサビリティで管理を厳密に行うためには、製造リードタイムが増える可能性があります。たとえば、製造品の部材や中間品をシリアルナンバーで管理したり、2次元コードのラベルやタグを貼付してハンディターミナルで読み取りしたりする必要があるからです。
作業工数が増え、業務プロセスが複雑化することで、全体の業務効率や作業効率が低下する可能性もあります。従業員への負担なども考え、製造現場の規模にあわせて無理のない範囲からトレーサビリティに取り組むことが大切です。
トレーサビリティを向上させるには
最後に、トレーサビリティを向上させる方法について説明します。
各工程を正しく記録する
トレーサビリティを向上させるには、後からでも「どのように製品がつくられたか」「どのような流通経路でどのような取り扱いがされたか」を、正しく追跡できるようにすることです。
そのためには、各工程を正しく記録する必要があります。しかし、各工程を正確に記録することは容易ではありません。手っ取り早く記録しようとすると、作業者がチェックリストに記録するという方法がありますが、人が行うことであるため忘れや間違いが伴います。
トレーサビリティが必要となるのは、自工程を過ぎてから、後工程で問題が発生した時です。その時、問題が発生した製品の情報を振り返ろうとした時に、「記録していなかった…」「記録を間違っていた…」などの問題が起きてしまっては、トレーサビリティとして意味がありません。
記録を自動化する
作業者が記録を行うと忘れや間違いが伴うため、記録を自動化することがトレーサビリティの向上につながります。やむを得ず作業者が記録する場合でも、直接記入するような方法は行わず、カメラやバーコードリーダー等で記録しましょう。
また記録したデータは、デジタルデータでトレーサビリティシステムに登録するようにします。システムに登録することで、データの管理を行うことができると共に、データが欠落していないかチェックすることができます。
万が一、記録作業を忘れていたとしてもデータが欠落しているため、直ちに作業者に記録をするように警告を出すことができます。
トラブル発生時に情報共有をする
トレーサビリティの目的は、製品を安心・安全に提供するため、問題があった場合に迅速に原因を特定して改善することで、製品の品質向上を図ることです。
そのため、単に記録をすれば良いということではありません。トラブルが発生した時に記録したデータを速やかに確認できなければ、トレーサビリティを有効に活用しているとは言えません。速やかにデータを確認するためには、システム化して記録したデータのデータベースを構築します。
データベースについては、内部トレーサビリティの場合は自社だけでシステムを構築することができますが、チェーントレーサビリティの場合は、サプライチェーン全体で連携することが重要です。
まずはチェーントレーサビリティを意識して内部トレーサビリティを構築し、その後チェーントレーサビリティと連携することで、更なるトレーサビリティの向上を図ります。
トレーサビリティの導入時の改善例
トレーサビリティについてくわしく解説してきましたが、どのように取り組めばいいのかイメージしにくい人も多いため、2つのトレーサビリティ導入時の改善例をご紹介します。
製造業に限らず、多くの業種や業態が適用できる活用事例ですので、ぜひ参考にしてください。
例1:シリアルナンバーの印字
シリアルナンバーの印字とは、製品ごとに固有の番号を付与する方法です。製品ごとにレーザーでシリアルナンバーを刻印することで、製品を一個ずつ識別でき、製品の履歴を詳細に追跡することが可能になります。
ある食品製造業者では、製造日や賞味期限とあわせて、識別番号としてロット番号のみを刻印していました。しかし、同一ロット内での生産順がわからないため、個々の製品を識別することができませんでした。
そこで、レーザーマーカーを使用し、各製品にシリアルナンバーを印字するように変更したのです。シリアルナンバーの印字というトレーサビリティを導入したことで、製品ごとの履歴管理が可能となり、不良品が発生したときの原因究明が素早く行えるようになりました。
例2:検査画像データと検査結果の紐づけ
検査画像データと検査結果の紐づけとは、製品の検査工程で撮影された画像データとその検査結果を、関連付けて管理する方法です。2つの情報を紐づけることで、検査の精度や信頼性を高め、問題発生時の原因究明を行いやすくなります。
ある企業では、検査工程で撮影された画像データを単に保存するだけでなく、データベース化して検査結果と紐づけるシステムを導入しました。検査結果と検査時の画像を紐づけて長期保存するというトレーサビリティを実施したことで、後から振り返った際に、検査結果の妥当性を判断しやすくなったのです。
特定の製品の検査結果を確認する際に、対応する画像データをすぐに参照できるようになるため、品質管理の精度向上にもつなげられました。
トレーサビリティに関するよくある質問
トレーサビリティのよくある質問をご紹介します。
Q1.トレーサビリティを取るとはどういう意味?
トレーサビリティを取るとは、製造過程における各段階の情報を集めて記録し、追跡可能にするという意味です。具体的には、原料の仕入れや製品の出荷から、流通や販売までの各段階での情報を詳細に記録し、問題が発生した際に原因を迅速に特定できるようにすることです。
製品やサービスの生産過程や流通過程などの各段階の情報を収集・記録することで、品質管理が強化され、製品の安全性が確保されます。また、食品業界の「食品トレーサビリティ」や、医薬品業界の「医薬品トレーサビリティ」など、業界・業種や分野に特化したトレーサビリティの種類がいくつかあります。
Q2.トレーサビリティを向上させるには?
トレーサビリティを向上させるには、各工程を正確に記録し、記録を自動化することが欠かせません。手作業ではミスが生じやすいため、カメラやバーコードリーダー、電子タグのRFIDタグを読み込むRFIDなどを使い、デジタルデータとして記録すれば、データの抜けや漏れのチェックもできます。
また、システム化して記録したデータのデータベースを構築し、トラブル発生時に情報共有できるようにすることも重要です。
Q3.トレーサビリティとトレーサビリティーはどちらが正しい?
「トレーサビリティ」と「トレーサビリティー」の意味は同じですが、一般的には「トレーサビリティ」と表記されることが多いです。どちらを使用しても意味は通じますが、表記を統一することで、文書やコミュニケーションの一貫性を保てます。
現場帳票システム「i-Reporter」でトレーサビリティを実現しよう!
トレーサビリティは、消費者の安全・安心に関わる製品や商品において欠かせないものです。製造工程や流通過程に問題があると、回収やリコールだけではなく、法律で処罰を受ける恐れがあるため、適切な製造工程・流通過程であることを証明しなければなりません。
「i-Reporter」は、トレーサビリティの導入に役立ちます。紙の帳票をデジタル化し、カメラやバーコードリーダーでデータを自動収集することで、記入漏れや記録ミスを防ぎます。また、データはクラウドで一元管理されるため、迅速な情報共有が可能です。
帳票の管理はもちろん、生産管理システムやERPなどの他システムとの連携など、「i-Reporter」があれば自社に合ったトレーサビリティを実施できるのでおすすめです。
ほかにも、生産ラインや製造ラインの効率化、生産管理やリスク管理の可視化、注目のDX(デジタルトランスフォーメーション)やIoTの推進にも「i-Reporter」が役立ちます。「i-Reporter」の公式サイトでは、業種別の導入事例もご紹介しておりますので、ぜひ一度チェックしてみてください。
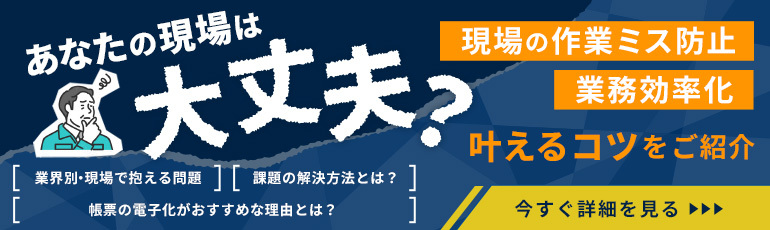

現場帳票研究所の編集部です!
当ブログは現場帳票電子化ソリューション「i-Reporter」の開発・販売を行う株式会社シムトップスが運営しております。
現場DXの推進に奮闘する皆様のお役に立てるよう、業界情報を定期的に配信致しますので、ぜひ御覧ください!