ポカミスとは、製造業界でよく使われる言葉で、一般的に不注意から起きる思いがけない失敗を意味します。
製造業の場合、ポカミスの発生が従業員のケガや商品の不良などにつながるおそれがあるため、事前に対策を講じることが大切です。
目次
そこで今回は、主に製造業におけるポカミスの要因やポカミス対策を実施する流れ、具体的な方法について解説します。
すぐに実践が可能なポカミス対策をご紹介しますので、製造現場の管理担当者様はぜひ参考にしてください。
ポカミスが起こる4つの要因
ポカミスの発生原因にはさまざまなものが考えられるものの、大きくまとめると4種類に分類が可能です。こちらでは、4つの要因について詳しく解説します。
人的な要因
ポカミスは、作業員に起因して発生するケースが多くあります。
これはヒューマンエラーとも呼ばれ、機械化やデジタル化、マニュアルの整備などによって対策が必要です。
ヒューマンエラーは主に2種類に分類されます。
1つ目は本人が意図しない記憶違いや認識の欠如が原因で発生するもの。うっかりミスと呼ばれることもあり、本人がミスとして認識していない場合もあります。
2つ目は従業員がルールを守らない場合や手抜きをしたときなどに起こるミスです。業務を特定の作業員に任せきりにしている現場で生じやすい傾向があります。
作業環境の要因
作業環境が悪い影響をもたらし、ポカミスにつながる場合もあります。例えば、作業環境にふさわしくない「照度」「騒音」「温度」などにより、作業員のスムーズな業務が阻害され、ミスの発生を誘発する可能性があります。
また、設備の不良もポカミスの原因です。製造現場の作業ミスを減らすには、適切な環境を整備することが大切になります。
作業手順の要因
作業方法が明確になっている場合でも、マニュアルや手順書に誤りがある場合はポカミスが発生しやすくなります。また、マニュアルに不備はないものの、作業手順が複雑な工程になっている場合も注意が必要です。従業員の理解が不足しやすく、ポカミスにつながる可能性が高まります。作業手順やマニュアルはできる限り簡単でシンプルなものに変更し、作業員に周知することでミスの発生率の低減が期待できます。
教育内容の要因
従業員に対する教育や研修の不足が原因でポカミスが発生しているケースもあります。知識やスキルが十分ではない状態で作業を行ったり、作業員ごとにやり方が異なったりすると、ポカミスが起きやすくなります。また、業務ルールそのものがきちんと定められていない場合も。職場での教育や研修は、ミス防止に欠かせない要素です。
ポカミス対策を実施する流れ【ゼロを目指した徹底ガイド】
ポカミスは、製品の品質低下や思わぬ事故、納期の遅延などを引き起こすため、迅速な対策が望まれます。こちらでは、ポカミス対策を実施する際の流れを7つのステップに分けてご紹介します。
Step1.ポカミスの原因を追究する
まずは、過去に自社で起こったポカミスの原因を確認しましょう。データ収集や作業員へのヒアリングを行い、ヒューマンエラーや作業環境など、どのような要因でポカミスが発生しているのかを特定します。ポカミスの原因を解明することで、効果的な対策を進めやすくなるでしょう。
Step2.作業環境や作業手順を一から見直す
次は作業環境や手順を見直しましょう。現場を直接確認するのはもちろん、作業員へのヒアリングの実施も効果的です。実際に作業を行う従業員目線で、問題点が明らかになることが期待できます。
Step3.従業員の意識を確認する
次のステップでは、作業をしている従業員がルールを守っているかどうかを確認します。現場の管理者が従業員の作業観察を行うと良いでしょう。
Step4.問題点の対策を進める
ここまでの手順によって、ポカミスが発生する具体的な要因が判明しているはずです。そこで続いては、ポカミスの要因ごとに対策方法を検討し、着実に実行していきましょう。例えば、曖昧になっている作業ルールを明確化する、チェックリストを活用して作業の抜けや漏れを防止する、仕事のしやすい作業環境を整備するなどの方法が効果的です。
Step5.改善点やルールを従業員に周知する
ポカミス対策の方法がまとまったら、教育や研修などの機会を設けて従業員に周知しましょう。作業環境を整備したり、手順のルール化を進めたりしても、従業員の理解が不足していると作業ミスの削減につながりません。改善点やルールが決まったら、作業員に周知し、徹底してもらうことで効果を高めましょう。
Step6.改善点やルールのテスト運用を行う
次は、改善点やルールを導入する前に、テスト運用を行って問題がないかをチェックします。テスト運用中は常に現場の状況を確認し、施策が現状のポカミス対策として適切かどうかを判断しましょう。思ったような成果を得られない場合や不備が見つかった場合には、改善策をアップデートし、最適化することが重要です。
Step7.改善点やルールの運用を開始する
テスト運用に問題がなければ、施策の本格的な運用を開始します。運用開始後も、継続的に従業員の作業や意識を確認し、改善策が現場に定着しているかを評価します。また、新たな問題が発生した場合は、適切な対応を行い、改善点やルールをさらに最適化していくのがポイントです。ポカミス対策は継続的な取り組みが求められるため、長期的な視点での改善活動を心がけましょう。
ポカミス対策に取り入れたい具体的な改善案
最後に、ポカミス対策として効果が期待できる改善案を3つご紹介します。ポカミスの要因や作業内容に応じて適切な対策を講じましょう。
指さし確認を実施する
指さし確認は、ポカミスの防止に有効とされています。作業前の緊張感を軽減したり、集中力を高めたりする効果が期待でき、不注意によるポカミスや事故の防止に役立ちます。
指さし確認を実施する際は、まず確認箇所を目視でチェックします。その後、対象物の名称を声に出しながら、指さしを行いましょう。次に、指さしを行った手を耳元に運び、頭の中で正しくチェックできているかどうかを確認します。問題がなければ「よし!」と発声しながら手を振り下ろして完了です。
指さし確認は、「ルールだから」と何となく行っても意味がありません。姿勢を正したうえでキビキビと動き、自分の耳にも聞こえるようにハッキリと発声することで目の前の作業に集中しましょう。
ダブルチェックを導入する
ダブルチェックは、1人が作業を行った後に別の人がチェックを行うことで、ミスを見逃さないようにする方法です。担当者が作業に慣れている場合、無意識のうちに「ミスはないはず」と思い込んでしまうケースがあります。ダブルチェックを実施することで、甘くなったチェックを最適化でき、ポカミスを事前に防止しやすくなるでしょう。ただし、ダブルチェックは時間やコストがかかるため、チェックリストを活用して作業を効率化したり、導入する範囲を慎重に検討したりする必要があります。
従業員教育マニュアルを作成する
従業員の教育不足によってポカミスが頻発している場合は、作業手順やルール、安全対策などをまとめたマニュアルを整備しましょう。新人教育や社内研修で活用することで、作業の統一化が図られ、ポカミスの発生を抑制できます。
ポカミス対策を徹底して安全で効率的な作業環境を実現しよう
今回は、ポカミスが起こる要因やポカミス対策を実施する流れ、具体例についてお伝えしました。ポカミス対策を成功させるには、原因を正確に把握したうえで、組織全体で改善に取り組むことが重要です。指さし確認やダブルチェックの実施、従業員教育マニュアルの整備などを通じてポカミス対策を徹底し、製造現場の品質向上やコスト削減を実現しましょう。
ダブルチェックに活用できるチェックリストやマニュアルの管理は、帳票の電子化システムである「i-Reporter」で行うと便利です。膨大な量の書類をすべてシステム上で管理でき、必要なタイミングでスマートフォンやタブレットからアクセスできます。ポカミス対策を促進しつつ、業務効率化に役立てられるため、興味がある場合はぜひお問い合わせください。
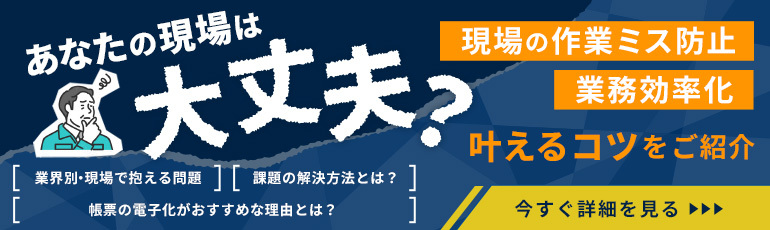

現場帳票研究所の編集部です!
当ブログは現場帳票電子化ソリューション「i-Reporter」の開発・販売を行う株式会社シムトップスが運営しております。
現場DXの推進に奮闘する皆様のお役に立てるよう、業界情報を定期的に配信致しますので、ぜひ御覧ください!