6シグマ(6siguma)とは、主に製造業で用いられている、品質管理におけるフレームワークです。
目次
統計学を用いて業務プロセスを改善し、製品やサービスの品質を向上させ、顧客満足度を高めることが目的です。最近では、製造業だけではなく、サービス業やIT業界など、さまざまな業界・業種で品質管理の重要性が高まっており、6シグマの品質管理手法が注目を集めています。
この記事では、6シグマの基礎知識と合わせて、メリットや導入する際のステップについてわかりやすく解説します。
6シグマ(6sigma)の基礎知識
業務改善を目的に6シグマの導入をお考えなら、6シグマがどのようなものなのかを正しく理解しなければなりません。はじめに、6シグマの基礎知識をご説明します。
6シグマとは?
6シグマ(Six Sigma)とは、品質管理におけるフレームワークで、統計学を用いて行われる改善手法の1つです。
主に、製造業で経営・品質管理の手法として利用されており、業務プロセスを改善し、製品やサービスの品質のばらつきを抑え、最適化を図ることが目的です。製品やサービスの品質のばらつきを減らすことで、欠陥のある不良品の発生を最小限に抑えられるため、顧客満足度の向上につながります。
品質や顧客満足度の向上が目的の6シグマは、製造部門だけでなく、営業部門や企画部門などでも用いられています。
6シグマの語源
6シグマの「シグマ(σ)」は、データのちらばり度合いを示す統計学用語の「標準偏差」の意味です。標準偏差とは、平均値からどれだけ離れているかを表しており、数値が大きいほどデータのばらつきも大きくなります。
6シグマとは、「6σ」=「不具合や不良品の発生を100万回のうち3~4回未満に抑えること」を目標としたことに由来しています。1980年代に誕生した6シグマは、その高い有用性から世界的に有名な大企業がこぞって導入し、最近では日本の企業でも広く取り入れられるようになりました。
6シグマのメリットと注意点
6シグマを用いることにはさまざまなメリットがある一方、いくつかの注意点もあります。導入する前に、6シグマのメリットと合わせて注意点も知っておきましょう。
6シグマのメリット
長期的な改善効果が期待できる
6シグマのメリットとして、6シグマを用いて製造工程や品質管理などの業務プロセスを改善することで、製品の安定化と標準化を図れることが挙げられます。たとえば、食品製造業の場合、原材料の分量や調理時間のばらつきを抑えることで、いつも同じ品質と味の製品の提供が可能です。
また、6シグマでは、データの収集と分析を継続的に行い、組織全体で改善サイクルに取り組み、品質の向上を図ります。6シグマを用いた改善は、個人の能力や発想に左右されるものではなく、組織の誰もが、6シグマを活用した改善をノウハウとして共有・蓄積できます。
改善サイクルを繰り返すことで、6シグマを活用した改善のノウハウが蓄積されるため、継続的な効果が期待できるのです。
汎用性が高い
6シグマは、業種や事業の規模を問わず活用できる手法です。製造業だけでなく、サービス業やIT業界など、さまざまな分野で導入されています。
たとえば、製造業では不良品の減少に活用されており、サービス業では顧客満足度の向上に活用されています。大企業はもちろん中小企業でも取り組みやすく、規模の大小を問わず効果を発揮できる、汎用性の高さがメリットです。
従業員がスキルアップを目指しやすい
6シグマのメリットとして、人材育成に役立つことが挙げられます。
6シグマを用いるためには、各部門を巻き込んだ議論が必要です。大勢と議論をすることで、進行能力や統括するための組織マネジメント力が身に付きやすくなります。
他にも、従業員との対話で磨かれるトーク力やコミュニケーション力、人脈が広がることで得られるスキルや知識なども身に付くため、従業員がスキルアップを目指しやすいメリットがあります。
顧客満足度の向上
6シグマを導入し、製品やサービスの品質を高めることで、顧客の信頼性を得やすくなることもメリットです。たとえば、電子機器製造業では、基板の精度が向上することで、デバイスの信頼性と寿命が延びます。
顧客の期待を超えるような高品質の製品・サービスの供給を目指せるため、顧客満足度を向上させ、リピーターの増加や新規顧客の獲得が期待できます。
6シグマの注意点
6シグマを導入する際の注意点が、従業員にかかる負担が見過ごされやすい点です。
6シグマのプロジェクトは、6シグマで問題を特定し、解決に取り組むという事実に基づくプロセスであるため、データ収集や分析、改善策の実施など、多くの作業を伴います。そのため、従業員に追加の業務負担がかかる可能性があります。
また、業務プロセスの改善時に、人にどのような影響を与えるのかという視点が抜けやすい点にも注意が必要です。6シグマは、業務プロセスの効率化や品質向上を目指すため、技術的な側面に焦点を当てがちです。しかし、改善策が従業員の業務内容や働き方に、どのような影響を与えるかを考慮しなければなりません。
6シグマを導入する際には、従業員の負担を軽減するためのサポート体制を整え、改善策が人に与える影響だけではなく、悪影響を与えた場合の対処方法も考えましょう。
6シグマと他の品質管理手法との違い
品質管理の分野には、6シグマの他にもさまざまな手法があります。なかでもとくに有名な2つの手法をご紹介します。
リーンシックスシグマ(Lean Six Sigma)
「リーンシックスシグマ(Lean Six Sigma)」とは、6シグマの統計的手法に、リーン生産方式を組み合わせた手法です。ばらつきを改善する6シグマと、無駄を改善するリーンを組み合わせ、ムラと無駄を排除して業務効率化を図ります。
6シグマとリーンシックスシグマの主な違いは目標です。業務プロセスのばらつきを抑えて品質を向上させる6シグマに対して、リーンシックスシグマはムダを排除して業務効率化を図ることが目標です。
トヨタ生産方式(TPS)
「トヨタ生産方式(TPS)」とはその名前の通り、トヨタ自動車が開発した生産管理手法です。徹底的にムダを排除し、業務の効率化や原価の低減を図るために編み出されました。
トヨタでは、「加工」「在庫」「不良や手直し」「手待ち」「作りすぎ」「動作」「運搬」の7つのムダを削減し、生産効率を向上してコスト削減を実現しています。
6シグマとトヨタ生産方式にはさまざまな違いがありますが、大きな違いが適用範囲です。多種多様な業界で活用できる柔軟性がある6シグマに対し、トヨタ生産方式は主に製造業での適用を想定しています。
6シグマの導入ステップ
6シグマは、「DMAIC(ディーマイク)」と言われる5つのステップで構成されています。DMAICは、「Define(定義)」「Measure(測定)」「Analyze(分析)」「Improve(改善)」「Control(管理)」の5つのステップの頭文字をとったものです。
6シグマを導入するためには、これらの5つの要素に取り組み、6シグマの基準を満たさなければなりません。6シグマの導入手順を5つのステップに沿ってご説明します。
Step1. Define(定義)
「Define(定義)」では、改善するプロセスの課題を洗い出します。
6シグマで最重要視しているのが、顧客の声(VOC)です。企業に寄せられた意見に加えて、SNSやECサイトのレビューなどの顧客の声をもとにして、不具合や顧客が不満に感じている製品やサービスを課題として定義します。
設定する目標は、具体的な数値でなければなりません。たとえば、「不良品が多い」という意見に対しては、「不良品率を10%から5%に減らす」のように、数値化した目標を立てましょう。
また、6シグマを導入するには、プロジェクトのリーダーである「ブラックベルト」が必要です。ブラックベルトとは、6シグマの高度な知識とスキルを持つ専門家で、組織全体の品質向上を目指し、他のメンバーと協力しながらプロジェクトを推進します。
シックスシグマのブラックベルトの役割は、プロジェクトの成功に向けて、さまざまな部分でアドバイスを行うことです。たとえば、製品の不良率を低減するプロジェクトでは、データを収集し、統計的手法を用いて、不良の原因を特定します。また、製造ラインの効率を向上させるために、作業手順の見直しや設備の最適化を提案・実施を行います。
6シグマの資格を取得するための試験は、海外でしか実施されていません。日本で資格を取得するには、6シグマのコンサルタント企業が実施するセミナーなどを受講し、企業独自の認定を受ける必要があります。
Step2. Measure(測定)
「Measure(測定)」では、製品やサービスの品質にとって重要な要素である「CTQ」を測定します。「Critical To Quality」の頭文字をとったCTQとは、顧客のニーズを満たすために必要な品質特性のことです。
また、現状を正しく理解するためには、具体的な数値を把握しなければなりません。たとえば、1日あたりの生産量や不良品の発生率など、数値で得やすいデータを収集します。
データを収集したら、表やグラフを用いて可視化しましょう。改善する業務プロセスを見える化することで、問題点の発見や評価をしやすくなります。
Step3. Analyze(分析)
「Analyze(分析)」で行うのは、問題の根本的な要因の特定です。具体的には、特定要因図といった「QC7つ道具」や、「なぜ」を5回繰り返して問題の根本原因を特定する「5Why分析」などを活用し、問題の原因を整理します。
Step4. Improve(改善)
「Improve(改善)」では、分析で特定した問題を改善するための方法を考えます。複数の改善案を出し、コストと効果のバランスを考慮して最も適した方法を選びましょう。
また、複数の改善案を同時に進めたり、2つ以上の改善案を組み合わせたりする場合は、それぞれの計画を小規模で試験的に実施するか、実験計画法の使用をおすすめします。改善が完了したら、既存の業務プロセスに一時的に導入し、効果を検証しましょう。
Step5. Control(管理)
「Control(管理)」で行うのは、改善した業務プロセスを継続できるようにする、定期的なモニタリングです。具体的には、従業員への教育や、誰でも改善できるように業務プロセスの標準化を行います。
また、新しいビジネスや商品、業務プロセスの設計段階には、6シグマではなく「DFSS」のフレームワークがおすすめです。DFSSは、「Define(定義)」「Measure(測定)」「Analyze(分析)」「Design(設計)」「Verify(検証)」の頭文字をとった、「DMADV」のフェーズを通じて進められます。
既存のプロセスの改善に用いる6シグマに対し、DFSSは新しい製品やサービスの設計に特化したものです。DFSSは、製品やサービスの開発段階から品質を重視し、顧客のニーズを満たすことを目指すため、品質確保やコスト削減などの実現につなげられます。
「i-Reporter」で6シグマをスムーズに導入しよう!
シックスシグマは、統計学を用いて製品のバラツキを小さくする改善手法で、製造業だけでなく他の業務改善にも幅広く活用されています。長期的な改善や人材育成が期待できるため、より良い製品やサービスの提供につなげられるでしょう。
現場帳票システム「i-Reporter」は6シグマの導入に役立つツールです。帳票管理をデジタル化すれば、データの収集・分析の効率化が図れます。
「i-Reporter」を導入すれば、情報の正確な収集や効率的なデータ分析などの機能により、6シグマのプロジェクトで必要なデータの収集と管理が簡単にできます。6シグマの導入と運用をサポートし、業務プロセスの改善と品質向上の実現に役立つ「i-Reporter」の導入をぜひご検討ください。
「i-Reporter」の公式サイトでは、必要な会員情報を登録するだけで、すべての機能を2か月無料でお試しいただける「無料トライアル」をご用意しております。活動記録の確認やフォローアップなど、実際の業務に使っていただくことで、機能の詳細や使い心地などを確認していただけるでしょう。
他にも、導入事例の掲載やお役立ち資料のダウンロードなど、導入前に必須との声が多い、さまざまなご要望に対応しております。貴社の課題に最適なソリューションをご提案しますので、お気軽にお問い合わせください。
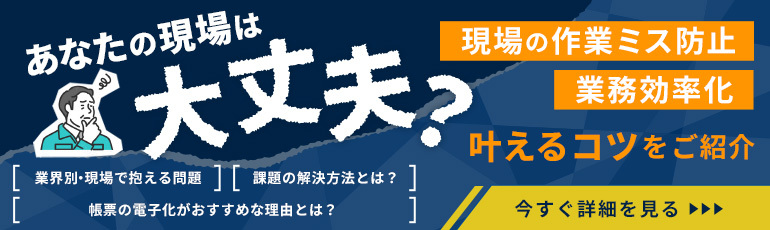

現場帳票研究所の編集部です!
当ブログは現場帳票電子化ソリューション「i-Reporter」の開発・販売を行う株式会社シムトップスが運営しております。
現場DXの推進に奮闘する皆様のお役に立てるよう、業界情報を定期的に配信致しますので、ぜひ御覧ください!