目次
歩留まり率は、生産品に占める良品の比率を示す指標です。製造業において生産性や品質、コストに直結する重要な概念として活用されています。
本記事ではそんな歩留まり率について、歩留まり計算の仕方や数値が低くなる要因と対策を含めて解説します。製造業に携わる方、とりわけ品質管理にかかわる方は、ぜひ以下を参考にしてください。
歩留まり率に関する基礎知識
まずは歩留まり率という用語の意味や重要性など、基本的な事柄を説明します。
歩留まり率とは?
歩留まりは「ぶどまり」と読み、英語では「yield(イールド)」と言います。生産数から出す良品の割合や投じた原料に対しての完成品の比率などを指します。
歩留まり率は、製品を作る際に投じた原材料に対し、そこから作られた製品の個数を示す割合のことです。いわば「良品ができる割合」であり、製造業における重要な指標のひとつとなっています。歩留まり率が高ければ、使用した原料や資源にロスがなく、生産能率が良いという理解ができます。
また製造業だけでなく、飲食業などさまざまな業種でも採用されている指標です。飲食業や食品業では、「歩留まり原価」や「歩留まり単価」といった応用概念も交えて、歩留り計算が原価計算に活用されます。水産業界では、魚の可食部と不可食部の歩合を調べる「歩留調査」といったものもあります。
歩留まり率はなぜ重要?
歩留まり率を高めることは、製造現場の生産性や効率性を高めるために重要です。作業が効率的であると評価する指標なので、歩留まり率の向上がすなわち生産効率の向上を意味します。
製品の品質やコストに直結するという観点でも、歩留まり率のチェックは大切です。一般的に歩留まり率を上げることは不良率を下げることであり、歩留まり向上は製造コスト削減に寄与します。
また歩留まり率は、現状把握や課題分析などにも利用されます歩留まり率の向上は良品の割合が増えることを意味するため、顧客満足度の向上に直結し、企業の競争力強化にとっても大切な要素です。
歩留まり率の計算方法
歩留まり率の計算式は、「歩留まり率(%) = 実際の成果数 ÷ 全体の総数 × 100」となります。成果数は完成品の数、全体の総数は投じた原材料の数と言い換えが可能です。すなわち歩留まり計算は、投じた原材料に対しての完成品の割合を示します。
例えば、投した原料数が100個で、完成品の数量が80個なら、歩留まり率は80%です。完成品の生産数量が50個なら、歩留まり率は50%と算出できます。
また成果数を良品数、全体の総数を完成品数と定義すると、歩留まり率は総生産量に占める良品の比率(=良品率)を表します。歩留まり計算を応用して、転用率や原材料費などを算出することも可能です。なお、歩留まり率の最高値は100%で、これは欠損品や不良品などのムダが全くない完璧な精度を意味します。
歩留まり率が低下する原因
歩留まり率の数値が低くなる要因として、以下の理由が挙げられます。
不良品が多い
作業の不備や設備の不具合などで不良品が発生しやすい傾向にあります。とくにヒューマンエラーやスキル不足といった作業者の不備、製造設備の不具合・故障、製造工程の煩雑さなどが、主な不良品発生の要因です。そのほか、気温、湿度、気圧などの環境条件も、不良発生に影響を与えることがあります。
不良率が上がると市場に出る商品数が減り、利益率の低下につながってしまいます。
原材料などの品質が低い
投入する原材料や使用している部品の品質がよくないと、完成品のクオリティにも影響が出やすいです。とりわけ原材料の扱いが不適切である、異物が混入しているなどの原因により、低質な完成品ができてしまう事例が散見されます。
また仕入れた原材料を一定期間保管しておく場合は、在庫管理に問題がある可能性も考慮すべきでしょう。
品質管理や生産計画に不備がある
品質管理や品質保証の体制ができていないと、製品のクオリティにばらつきが生じやすく、欠損品も発生しやすいでしょう。企業が品質管理についてずさんな考え方をしていると、歩留まり率の低下という結果に直結してしまうのです。
具体的には、検査に必要な設備などの不足、業務を標準化するルールが決まっていない、マニュアルの不徹底などの問題が、歩留まり率の悪化をもたらします。
歩留まり率の改善策
歩留まり率が低いと不良品や廃棄物などの無駄が増えてしまうため、数値を高めるための対策を講じる必要があります。以下では効果的な改善方法をいくつか紹介するので、ぜひ貴社に合った対応策を考えるヒントにしてみてください。
歩留まり率を低下させている原因を特定する
原因を特定し、それに合わせた改善目標を設定することが重要です。歩留まり低下の原因は生産ラインの問題や品質基準の不備などさまざまであり、ケースごとに取りうる施策も違います。
また原因に沿った改善目標を設定したら、改善し続ける意識を常に持つことが不可欠です。
4Mの観点から状況を整理する
4Mとは、Man(人)、Machine(機械)、Material(材料)、Method(方法)のことを指します。さまざまな観点・部分から分析を行うことがより良い改善のポイントです。
具体的には、人材教育、機械設備のメンテナンス、原材料の品質管理、作業手順などの改善点を洗い出すことで、製造プロセスの効率化が期待できます。また生産管理システムのDXを実現し、4Mのデータや情報を一元管理するというのもより良い解決策です。
改善を目指しTPM活動を行う
TPMとはTotal Productive Maintenanceの略で、日本語では「全員参加の生産保全」などと訳されます。TPM活動は、人や設備に着目し、生産プロセスにおけるあらゆるミスやロスをなくすことを目指す取り組みです。
TPM活動は、歩留まり率の低さを是正するのに役に立つマネジメント手法となります。具体的には、OJTの実施、QC工程表の作成・運用、マニュアルの整備及び定期的な手直し、生産状況をリアルタイムで可視化などの対策が有効です。
OJTとは「On-the-Job Training(オンザジョブトレーニング)」の略で、自社の上司や先輩が指導役となる従業員研修のことを指します。 またQC工程表とは、原料の入荷から製品の出荷に至るまでの一連の生産工程について、フェーズごとに品質管理の方法や項目を記載したツールのことです。
歩留まり率を高める施策で生産性の向上を!
「完成品に占める良品の割合」を示す歩留まり率が高いことは、生産性や品質が高いことを意味し、品質向上はもちろん製造コスト削減にも直結します。反対に歩留まり率が低さは、不良率の高さや管理体制の不備といった課題を示唆するため、適切な改善策を講じるべきです。
歩留まり率の改善方法は原因によってさまざまですが、ITツールの導入による業務効率化も有益な施策になりえます。例えば、現場帳票システム「i-Reporter」では、製造現場の日報・報告書業務をペーパーレス化し、記録や転記のミスを大幅に削減できます。現場作業員のヒューマンエラーを減らすことで、歩留まり率の改善が可能です。
またi-Reporterは在庫管理・倉庫業務もデジタル・IoT化できるため、原材料の品質管理という観点から歩留まり向上を実現できる可能性もあります。さらにi-Reporterは既存の生産管理システム等との連携も簡単で、導入しやすいこともおすすめのポイントです。歩留まり率の改善策としてITツールの導入をご検討の方は、ぜひi-Reporterを選択肢に入れてみてください。
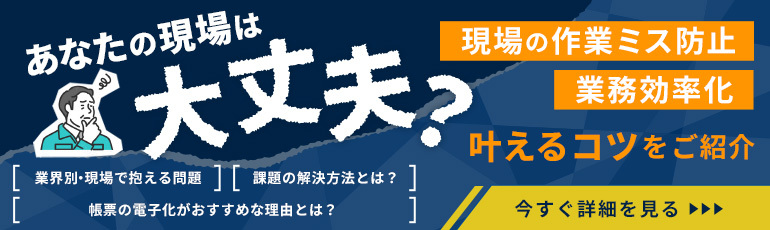

現場帳票研究所の編集部です!
当ブログは現場帳票電子化ソリューション「i-Reporter」の開発・販売を行う株式会社シムトップスが運営しております。
現場DXの推進に奮闘する皆様のお役に立てるよう、業界情報を定期的に配信致しますので、ぜひ御覧ください!