目次
「設計段階で品質やコストの問題を解決したい」「製造工程の潜在的なリスクを事前に把握する方法を知りたい」「ヒューマンエラーによる不具合発生を防止したい」「設計変更に伴うリスクを最小限に抑えたい」 このような悩みをお持ちではありませんか?
こちらの記事では、製品の開発や製造工程におけるリスクマネジメントの手法である「FMEA」(Failure Mode and Effects Analysis:故障モード影響解析)について解説します。
FMEAの概要や具体的な実施の流れ、よくある質問まで、図やテンプレートを用いながら解説していくので、ぜひ導入の参考にしてみてください。
FMEAの概要
FMEAとは、製品や製造工程における潜在的な故障を特定し、その影響を分析するための体系的なアプローチです。
主に製品設計や製造工程の段階で実施され、品質向上やリスク低減に役立ちます。
FMEAとは
FMEA(Failure Mode and Effects Analysis:故障モード影響解析)は、製品やプロセスにおける潜在的な故障モードを特定し、その影響を分析するリスク評価の手法です。
故障モードとは、製品やプロセスがどのように故障する可能性があるかを具体的に示したものです。例えば、「部品の破損」「システムのエラー」「ヒューマンエラー」などがあります。
設計段階で製造工程のリスクを予測し対策を検討することで、製品の品質や信頼性を向上させることを目的としています。
FMEAの分類
FMEAは、対象とする範囲や目的によって、いくつかの種類に分類されます。ここからは、主要な3つのFMEAについて見ていきましょう。
工程FMEA
工程FMEAは、製造工程で発生しうるトラブルを予防するための手法です。設備や作業者、材料、手順など、製造工程における様々な要素を対象として、それぞれの要素に潜む故障モードを抽出します。
工程FMEAを実施することで、製造工程の品質や生産性の向上、コスト削減などが期待できるでしょう。
設計FMEA
設計FMEAは、製品設計の段階で実施されます。製品の設計に潜む故障モードを特定し、その影響を分析することで、設計の欠陥を早い段階で発見し、修正することが目的です。
設計FMEAを実施することで、製品の信頼性や安全性の向上、開発期間の短縮、コスト削減などができます。
機能FMEA
機能FMEAは、製品やシステムの機能に着目したFMEAです。製品やシステムが本来備えているべき機能が、どのような原因で失われるかを分析し対策を検討します。
機能FMEAを実施することで、製品の機能性や信頼性の向上、顧客満足度の向上に繋がるでしょう。
FMEAのメリットやデメリット
FMEAを導入することで、問題点を事前に洗い出し、対策を立てることができます。 その結果、品質向上やコスト削減などのメリットが期待できますが、一方でデメリットも存在します。ここからは、FMEAのメリットとデメリットをそれぞれ詳しく紹介します。
FMEAのメリット
FMEAを導入することで、以下のようなメリットがあります。
• 量産体制を作る前のリスク対策が可能
• 顧客満足度の向上
• 人的リソースやコストの最適化
ここからは、3つのメリットについて詳しく見ていきましょう。
量産体制を作る前のリスク対策が可能
FMEAを導入することで、量産体制を作る前に潜在的な故障モードを把握することができます。
リスクに応じた対策を事前に知ることで、量産開始後の不具合発生を大幅に減らすことができるため、修正コストの削減につながるでしょう。
顧客満足度の向上
FMEAの導入により製品の品質を向上させ、トラブルを未然に防ぐことで、顧客満足度を高めることが可能です。
人的リソースやコストの最適化
事前にリスクの発生を防ぐことで、対応コストを抑えることでトラブル発生時の対策コストを削減できます。
トラブルが発生すると、その対応に多くの時間や費用を費やすことになりますが、FMEAによって事前にリスクを排除することで、人的リソースやコストを最適化することができるでしょう。
例えば、設計変更に伴うリスクをFMEAで事前に洗い出し、対策を講じることで、手戻りや修正によるコスト増加を防ぐことができます。
また、ヒューマンエラーによる不具合発生の可能性を分析し、作業手順の見直しやチェック体制の強化などの対策を立てることで、人的ミスを減らし、品質向上に繋げることが期待できるでしょう。
FMEAのデメリット
FMEAには、主観的な評価になりやすいというデメリットが存在します。担当者の経験や知識に基づいて評価を行うため、どうしても主観的な評価になりやすいという側面があるのです。
担当者が1人の場合、故障モードの想定が限られる可能性もあるため、複数人でFMEAの評価を行うことで、より客観的な評価に近づけることができるでしょう。
FMEAの評価フォーマットに記載する項目の例とテンプレート
FMEAを実施する際には、専用のフォーマットを用いるのが一般的です。ここでは、FMEAのフォーマットに記載する項目の例と、無料でダウンロードできるテンプレートを紹介します。
FMEAの記載項目の例
FMEAのフォーマットには、一般的に以下の項目が記載されます。
記載項目 | 概要 | 記載の例 |
対象 | 故障モードの対象を記載する | 製品A、製造工程B、作業員Cなど |
故障モード | 想定される故障モードを具体的に記載する | 部品の破損、システムのエラー、作業ミスなど |
故障の原因 | 故障モードが発生する原因を具体的に記載する | 設計ミス、材料の欠陥、操作手順の誤りなど |
影響度 | 故障モードが発生した場合の影響の大きさを数値化して記載する | 機能停止、生産ラインの一時停止など |
発生頻度 | 故障モードが発生する頻度を数値化して記載する | 高度、中度、低度 |
検出難易度 | 故障モードを検出ことの難易度を数値化して記載する | 容易、中程度、難しい |
RPN | 影響度、発生頻度、検出難易度を掛け合わせた数値(リスク優先度)を記載する | RPN = 影響度 × 発生頻度 × 検出難易度 |
このフォーマットを用いることで、FMEAは体系的なリスク管理が可能です。
FMEAのテンプレート
下記より、FMEAのテンプレートをダウンロードして、実際に使用することができます。
オリジナルのFMEAテンプレートを活用し、実際の業務に取り入れてください。詳細は<FMEAのテンプレート>からダウンロードできます。

FMEAの実施手順
FMEAは、以下の手順で実施することで、効果的にリスク分析を進めることができます。
- FMEAフォーマットの作成
- 故障モードの記入
- 影響度の記入
- RPN(Risk Priority Number:危険優先度)の計算
- 改善計画の立案と実施
ここからは、FMEAの基本的な実施手順を5つのステップに分けて解説します。
Step1.FMEAフォーマットの作成
まずは、FMEAを実施するためのフォーマットを作成しましょう。
FMEAの対象を明確にした上で、必要な項目を盛り込んだフォーマットを作成することで、情報を整理しやすくなり、後続のステップで情報を管理しやすくなります。
Step2.故障モードの記入
FMEAの対象となる製品や工程ごとに、想定されるリスクを洗い出し、フォーマットに故障モードと影響を記載していきましょう。
Step3.影響度の記入
故障モードによって発生するリスクを、定量的に評価します。影響度、発生頻度、検出難易度の3つの項目について、客観的な基準を設けた上で数値化していきます。
Step4.RPN(Risk Priority Number:危険優先度)の計算
影響度、発生頻度、検出難易度という3つの要素を数値化し、掛け合わせることで算出されるRPN(Risk Priority Number:危険優先度)は、リスクの優先順位を定量的に示す指標です。RPNは、リスクの大きさを示す指標ですので、RPNが高いものから優先的に対策を検討する必要があることを示しています。
Step5.改善計画の立案と実施
RPNの高い故障モードに対して、その発生頻度を低減したり、影響度を抑制したりするための改善計画を立案します。改善策を実施した後は、再度FMEAを実施して、リスクが低減されていることを確認しましょう。
FMEAに関するよくある質問
FMEAについて、よくある質問をまとめました。
FTA(Fault Tree Analysis:故障の木解析)とは?
FTA(Fault Tree Analysis:故障の木解析)とは、製品やシステムの故障が発生する原因を、視覚的に分析するための手法です。
製品の故障など、起こってほしくない事象をトップイベントとして設定し、そのトップイベントに繋がる原因を、論理記号を用いてツリー状に展開していきます。
FTAでは、故障の木図(FT図)を作成することで、トラブルとリスクの因果関係を視覚的に分析することができます。

DRBFM(Design Review Based on Failure Mode:故障モードに基づく設計レビュー)とは?
DRBFM(Design Review Based on Failure Mode:故障モードに基づく設計レビュー)とは、FMEAで抽出された故障モードに基づいて、設計の妥当性を検証する設計審査のことです。
DRBFMでは、設計担当者だけでなく、品質保証や製造などの関係者が集まり、設計の妥当性や問題点、改善策などを目的としています。
FMEAを活用した効率的なリスク管理
この記事では、FMEAの概要やメリット・デメリット、具体的な実施手順について解説しました。
FMEAは、製品開発や製造工程における潜在的なリスクを特定し、未然に防ぐためのツールですが、FMEAはあくまでツールの一つであり、その効果を最大限に発揮するためには、適切な運用が必要です。
シムトップスのi-reporterは、FMEAの実施を効率化し、より正確なリスク評価を可能にするツールです。 豊富なテンプレートや分析機能を活用することで、経験が浅い担当者でもスムーズにFMEAを実施できます。
また、i-reporterはクラウドベースのシステムですが、オフラインでも使用可能です。そのため、場所や時間にとらわれず、インターネット環境が不安定な場所でも、チームで共同作業を行うことができます。
社内にFMEAの専門知識を持つ人材がいない場合は、i-reporterの導入とあわせて、シムトップスのコンサルティングサービスをご利用いただくことも可能です。
FMEAを適切に活用することで、製品やサービスの品質向上、顧客満足度向上、コスト削減を実現できる可能性があります。ぜひ、この記事を参考に、i-reporterを活用したFMEAをビジネスに取り入れてみてはいかがでしょうか。
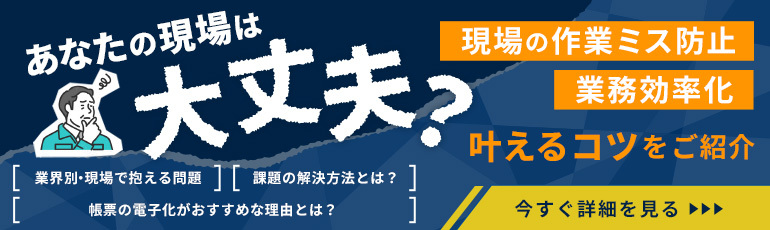

現場帳票研究所の編集部です!
当ブログは現場帳票電子化ソリューション「i-Reporter」の開発・販売を行う株式会社シムトップスが運営しております。
現場DXの推進に奮闘する皆様のお役に立てるよう、業界情報を定期的に配信致しますので、ぜひ御覧ください!