For those who want to streamline daily production reports in manufacturing sites:
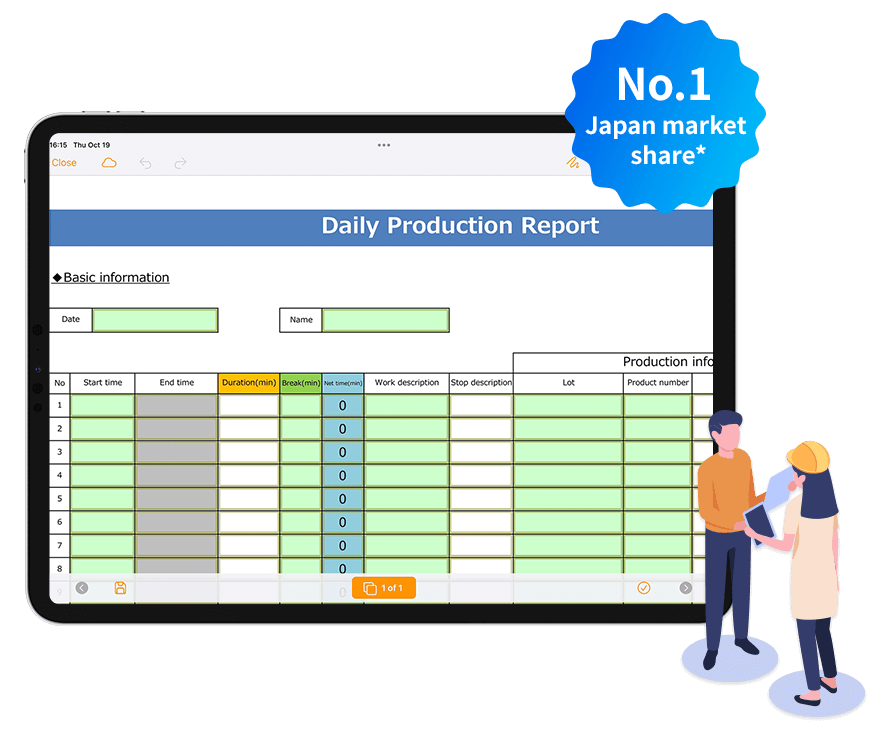
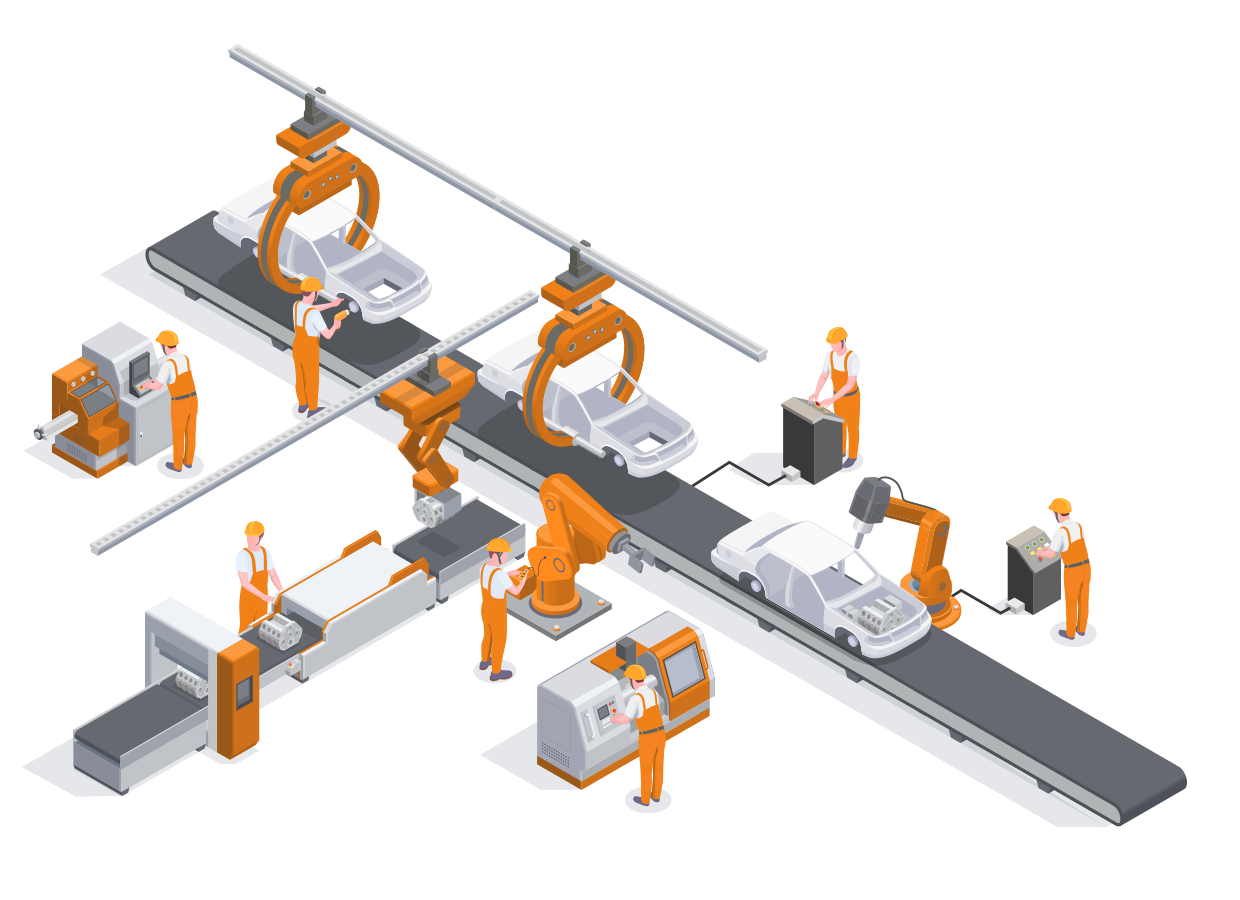
- Real-time detection of on-site conditions!
- Standardization of work processes and
significant reduction of input errors and mistakes! - Integrate with other systems for analysis and optimization!
*Source: Fuji Chimera Research Institute, issued on August 8, 2023. Achieved sustainability by SX/GX , Current status and future prospects of ESG support
related
markets
ⅡーAー10 on-site report paperless solution market share of 48.4% (based on actual results for fiscal year 2022).
Adopted by more than 4,000 Companies!
No.1 market share in paperless applications.
Manufacturing workers and managers
Do any of these concerns occur when creating and reporting daily reports?
- Paper is messy and hard to read making it difficult to check contents
- Calculation errors causing misinformation to be recorded
- Difficult to ascertain current situation without checking directly with factory personnel
- It takes time to transcribe and aggregate daily report data.
- Unable to manage costs properly due to an inability to accurately track man-hours
- The storage location of daily reports has expanded and management has become more complex.
For all these concerns
and more,

has got you covered!
The digitization of on-site work documents allows
for automated data aggregation and daily report creation.Contact us to learn more
Unique selling point of
Convert your field work reports into digital format!
Digitize without the need to overhaul your paper-based work flows
The style of the paper form can be directly imported as the input screen on the tablet. The field workers can simply enter the information as they would with the paper form, and the daily report will be completed automatically.
Unique selling point of
Easy and accurate input is possible via intuitive operation!
Enables speedy input and a significant reduction in omissions, errors, and inconsistencies in format.
Paper-based daily reports often result in problems with input time and variations in format from person to person. With i-Reporter, anyone can easily and accurately create a daily report using features such as input error prevention and input assistance.
Unique selling point of
Aggregate and analyse daily report data with ease!
The daily report data is managed in a database and can be used for a variety of purposes.
Daily reports entered on the tablet are stored and managed in a database and can be exported in EXCEL, PDF and CSV formats, making it possible to improve the efficiency of aggregation work and utilise the information in business systems and analysis tools.
Unique selling point of
Grasp real-time on-site information in the here and now
Real-time monitoring of on-site progress and productivity.
Data registered on the server can be checked in real time from the office or other locations, enabling swift delegation and decision-making
Unique selling point of
Advanced daily reporting and analysis via external system integration
Data can be automatically linked to production management systems, ERP and other systems.
Work order information can be displayed in i-Reporter and performance data can be linked to production management systems and more. It is also possible to aggregate and track cost management and other tasks in real-time, something that is historically difficult to do with paper forms.
Main Functions
-
Form creation
and entryOn-site operators can enter data easily, without strain and without errors via easy-to-read and easy-to-understand forms.
-
Form Design
(creation of templates)Familiar Excel forms can be converted directly into digital forms. Following implimentation, users can easily change the layout of the forms and add additional items via Excel.
-
Form
ManagementThe data for the forms created is centrally managed by the system, and the forms can be viewed, edited and exported via the web management screen. User rights management and security measures are also in place.
-
Integration with
other systemsThe system provides robust data integration capabilities with external systems. It automates processes such as aggregation, reporting, and analysis after report input, greatly improving operational efficiency.
Specially recommended features for daily reporting
Extensive suite of data entry features
A number of input method formats are available, including text, numbers, multiple choice and dates. Data entry via bar codes and QR codes is also possible.
As well as reducing the variation in data entry formats and errors by individual workers, it also speeds up input and makes work more efficient.
Data entry time recording
The time when forms are issued and saved and when each work item was entered can also be recorded automatically.
The system can also be used to analyse and improve work content as well as making it easier to manage work history by showing the time spent on data entry by each worker.
Peripheral device integration
(microphones, measuring devices, NFC, RFID, Bluetooth)
Users can also link i-Reporter to a number of peripheral devices, such as microphones for voice input, barcode readers and digital measuring devices, enabling input in a wide variety of ways that would be otherwise unachievable via paper.
PLC Integration
Information from PLCs can be captured automatically, preventing data omissions and numerical entry errors.
Users can also reduce post-processing man-hours, such as transcribing to Excel as well as time heavy aggregasion and data entry into core systems. Equipment data can be
easily grasped and processed in forms, improving the speed and accuracy of data analysis.
Adopted by more than 4,000 Companies!
No.1 market share in paperless applications.
Field Report Digitization System
for Automating Daily Report Creation for the Manufacturing Industry
Contact us to learn more
On-site customer testimonials
After implementing
i-Reporter,
the time taken to create daily reports went from
80 minutes to zero minutes.
For some time now, the management of the huge number of paper daily work reports generated at the production site and the data entry of these reports has taken an enormous
amount of time. In addition, input errors during the transcription process were also a major concern.
The deciding factor which lead to the implementation of i-Reporter was the fact that the system can be used without any special skills and that you're able create forms
without the need of time-consuming programming.
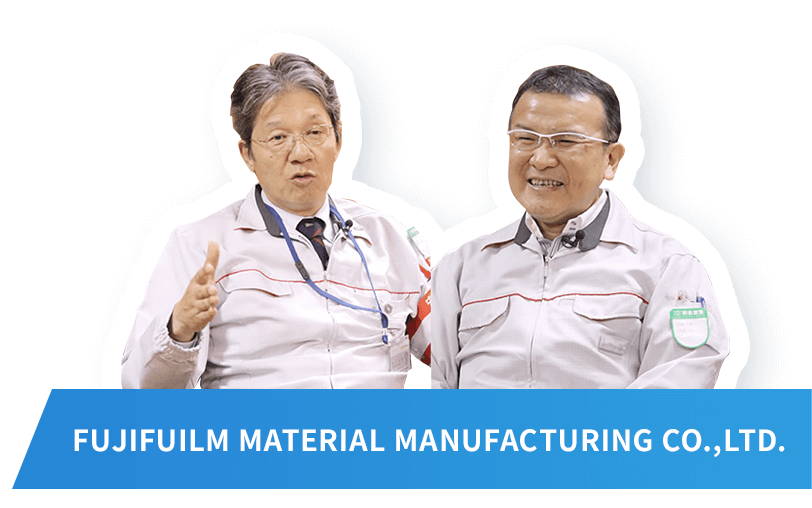
We were not satisfied with merely shifting to digital, and made requests for a more convenient and efficient system that doesn't use paper. Specifically, we asked for the incorporation of functions that enable input via list selection and automatic transition to the next item, without the need for a keyboard. When the system was first introduced, there was some resistance in the field, but today, the overwhelming response, including from senior staff, is that it is more convenient and easier to use than paper. Digitisation has automated the creation of daily reports, eliminating the need for work that used to take upwards of 80 minutes. We are very satisfied with the significant reduction in man hours and the ability for real-time situational analysis.
achievements
Adopted by more than
4,000 Companies!
No.1 market share in paperless applications.
-
cocument creation and management solutions sector of the ConTech market
No.1 domestic market
share of 42.3% among2021.05.18 Deloitte Tohmatsu MIC Research Institute "Contech Cloud Solution Market Actual Conditions and Outlook 2021 Edition"
-
Paperless on-site
form solutionDomestic market volume
Top market share of 48.4%!References: As researched by Fuji Chimera Research Institute, Inc. in Feb. YEAR of ICT Revolution during the Covid-19 Pandemic
-
Implementation Results
Number of contracted users:
196,207 users!(As of Aug, 2024)
-
ConMas i-Reporter
Over 4,000
onboarded companies(As of Aug, 2024)
Implementation Steps
We would be more than happy to explain the product and give you a demonstration before you consider implementing it. We will provide full support from specific consultation at the consideration stage through to implementation and operational support. Please feel free to contact us for more information.
-
-
Product explanation seminar
-
Product
workshop &
Free trial
Free trial -
Contract
signing -
Service start/
Support
Frequently Asked Questions
What types of system are available?
The system can be provided either as a cloud service or on-site product. Please select the option that best suits your needs. Feel free to contact CIMTOPS or your distributor for more information.
Is it possible to trial the system before implementation?
Up until the end of March 2022, up to 100 users will be able to use all functions free of charge for up to three months as part of the "Support for work style reform and
telework" programme. The trial can be selected either via the cloud or on-site versions.
For more information, go to the i-Reporter
free trial page .
Do you offer training courses or how-to-use workshops?
There are many distributors in each country and they can provide the training courses and technical supports. For details, please contact CIMTOPS or your distributor.
Can it be integrated with our own existing business system and various other cloud services?
It is possible to integrate our product with various business systems and various cloud services using the API and ConMas Gateway for external system integration. For details, please contact CIMTOPS or your distributor.

About Us
CIMTOPS Corporation is a Japanese software maker with a proven track record for making software to help companies in the manufacturing industry move to digital solutions such as production control schedulers, process control systems,
and on-site digital reporting software.-
For individual order manufacturing
Production scheduler & Process management system
-
BOP (Bill of Process) tool
- Company name
- CIMTOPS Corporation.
- Established
- October 1, 1991
- President and CEO
- Takashi Mizuno
- Headquarters
-
Shin-Meguro Tokyu Building 10F, 2-25-2 Kami-Osaki, Shinagawa-ku, Tokyo 141-0021, Japan
TEL: 03-5721-4610
FAX: 03-3491-4610
- Other offices
- Chubu Area (Kariya) & Kansai Area (Kyoto)
- Overseas
- CIMTOPS (Shanghai) Information Technology Co. & CIMTOPS SG LAB Pte.
Our Customers
Adopted by more than 4,000 Companies!
No.1 market share in paperless applications.
Field Report Digitization System
for Automating Daily Report Creation for the Manufacturing Industry