Work such as warehousing,
inventory and picking
can be made labour-saving and efficient.
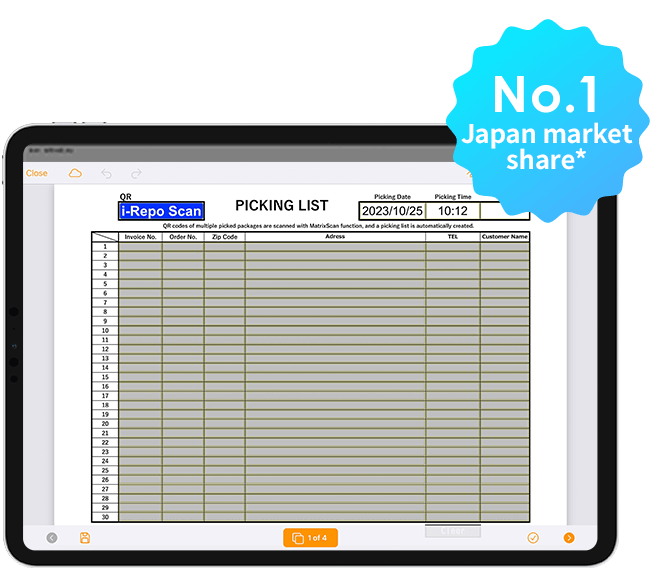
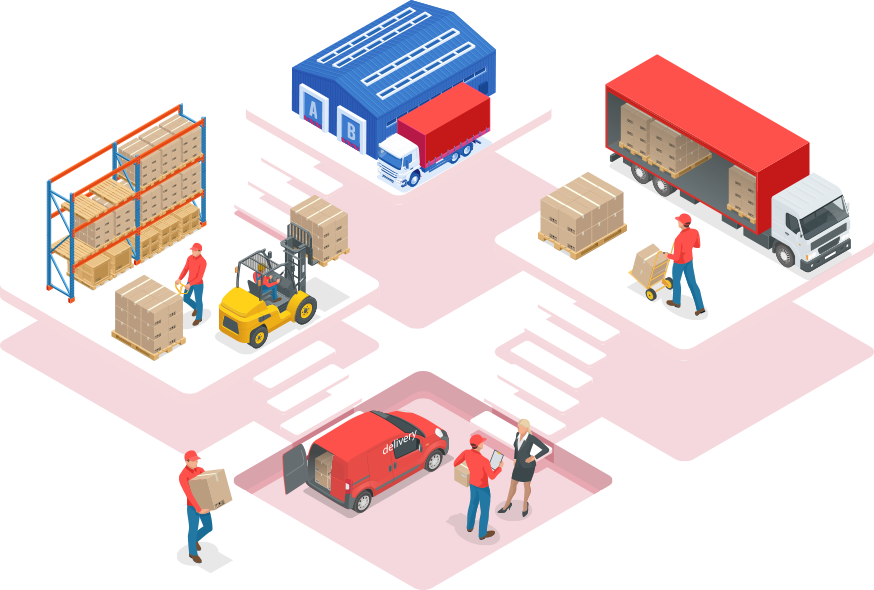
- Less than 1/5 the implementation cost of a handheld terminal!
- Accurate input operations are achieved/errors are drastically reduced in warehousing, shipping and inventory operations!
- Batch & continuous barcode scanning functionality makes picking super-efficient!
*Source: Fuji Chimera Research Institute, issued on August 8, 2023. Achieved sustainability by SX/GX , Current status and future prospects of ESG support related markets
ⅡーAー10 on-site report paperless solution market share of 48.4% (based on actual results for fiscal year 2022).
Logistics and warehousing operations in the manufacturing industry...Do you have any of these problems?
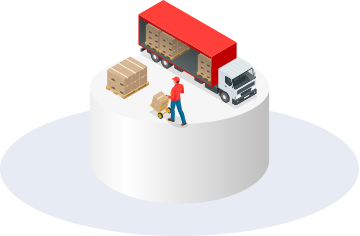
Inbound and Outbound delivery
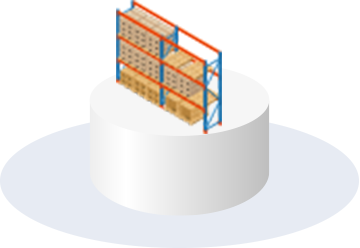
Inventory Control
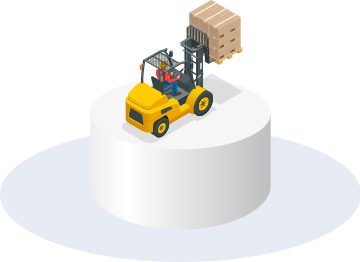
Stocktaking
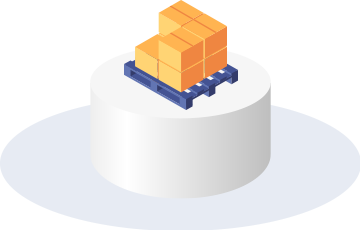
Order picking
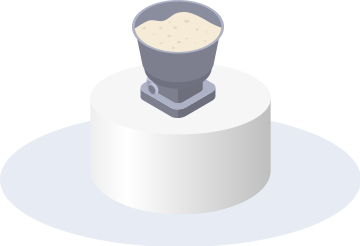
Raw material deposit
- Errors, omissions, and variations in formatting are common due to the need for visual confirmation of each item on the checklist during the checking process.
- Difficulty in transcribing from paper managed charts to other systems.
- There are many order picking errors and shipping errors, resulting in claims from the delivery destination.
- The introduction of handheld devices or systems is expensive and not progressing.
- The work is laboursome because the barcodes are read one by one.
solves all these issues!
Work such as warehousing, inventory and order picking
can be made labour-saving and efficient.
Digital On-Site report system
Contact us to learn more
Advanntages of
Achieve operational efficiency through continuous batch barcode scanning!
Streamline manual tasks with lightning-fast barcode scanning capabilities, eliminating the need for one-by-one visual confirmation!
Efficiently scan multiple barcodes in succession by displaying them on the screen and scanning them in batch, allowing for continuous scanning!
Even with
a large quantity of mixed barcodes of different types, it is possible to only scan the barcodes that have been pre-specified, ensuring accurate and efficient barcode
scanning.
Regular inventory checks and order picking tasks can be dramatically sped up using this barcode scanning feature.
Advanntages of
By identifying barcodes that do not match the specified conditions, this feature prevents errors in tasks and ensures accuracy.
Preparing a list in advance allows the scanning feature to instantly identify and distinguish barcodes, making the process quick and efficient.
Preparing a pre-defined list of barcodes in advance also makes it possible to verify the accuracy of planned and actual readings.
The barcode scanning
function, alerts users to non-existent barcodes via a red color display and beep sound, preventing reading errors. This intuitive and error-free operation allows for
increased accuracy and efficiency.
*Note: i-Repo Scan is required.
Advanntages of
Eliminate the need for manual data entry with seamless data integration with higher-level systems!
Real-time data reflection in the upper-level systems allows for immediate visibility of the on-site situation.
By simply inputting work progress and achievements into a tablet, data can be automatically reflected in other systems eliminating unnecessary transcription work and
allowing for real-time visibility of the situation.
The decrease in transcription errors also minimizes the discrepancy between theorized inventory and actual
inventory.
*Note: Development for integration with other systems is required.
Advanntages of
Input screens can be created easily by anyone via no-code!
Feedback from the job site can be quickly reflected in reports, leading to greater speed of improvements.
You can directly import Excel-created form layouts into the system and reflect them as-is. This allows you to digitize familiar on-site reports without
the need for operation instructions such as input methods.
Maintenance of forms can also be done in-house, resulting in significant cost and time savings when making
amendments.
Advanntages of
Eliminates the need for expensive dedicated handheld devices!
Compared to traditional systems that utilize handheld devices, the introduction cost is less than 1/5!
i-Reporter is an app that can run on iPad, iPhone, and Windows (*Note), so there is no need for dedicated devices such as handheld devices. With the ability to create barcode scanning apps without code and develop system integration, the cost of system implementation using traditional handheld devices can be reduced to less than 1/5 of the previous cost.
*Note: Barcode scanning using the camera is not available on Windows tablets.
Deployed by more than 4,000 companies!
No.1 share in paperless applications.
Work such as warehousing,
inventory and picking can be made labour-saving and efficient.
Digital On-Site report system
Contact us to learn more
Main Functions
-
Form creation
and entryOn-site operators can enter data easily, without strain and without errors via easy-to-read and easy-to-understand forms.
-
Form Design
(creation of templates)Familiar Excel forms can be converted directly into digital forms. Following implimentation, users can easily change the layout of the forms and add additional items via Excel.
-
Form
ManagementThe data of created report forms is centrally managed within the system, and users can view, edit, and output reports through a web-based management screen. User access permissions and security measures are thoroughly implemented to ensure data security.
-
Integration with
other systemsThe system provides robust data integration capabilities with external systems. It automates processes such as aggregation, reporting, and analysis after report input, greatly improving operational efficiency.
Recommended featuresfor logistics and warehouse operations in the manufacturing industry.
Learn by watching
Barcode Scanning
Quantity Counting Feature with Batch & Continuous Barcode Scanning
The quantity counting feature with batch and continuous barcode scanning allows for efficient inventory checking and verification during stocktaking or inbound/outbound operations. The scanned barcode content and counted quantity are displayed on the screen, allowing workers to intuitively confirm the barcode content and quantity. The scanned data can also be accumulated within the report for further processing.
Extensive suite of data entry features
i-Reporter provides a wide range of digital input options such as text, numbers, multiple choice, dates, and master data, as well as voice input. By utilizing threshold judgment and mandatory input settings, it is possible to reduce mistakes and omissions in data entry, improve input speed, and streamline business processes for increased efficiency.
Automatic Calculation
i-Reporter allows you to set up calculation formulas such as basic arithmetic operations, and the system automatically calculates the results. There is no need for mental calculations or using a calculator, reducing the risk of calculation errors.
Peripheral Device Integration
(microphones, measuring devices, NFC, RFID, Bluetooth)
Users can also link i-Reporter to a number of peripheral devices, such as microphones for voice input, barcode readers and digital measuring devices, enabling input in a wide variety of ways that would be otherwise unachievable via paper.
Deployed by more than 4,000 companies!
No.1 share in paperless applications.
Work such as warehousing,
inventory and picking can be made labour-saving and efficient.
Digital On-Site report system
Contact us to learn more
On-site customer testimonials
After implementing i-Reporter,
inventory management tasks
were reduced by 90% from
840 minutes per month to
84 minutes.
With the introduction of i-Reporter, inventory management tasks that were previously paper-based can now be easily inputted on iPads. Furthermore, the synchronization of inventory quantities between i-Reporter, the core system, and the production management system has eliminated the need for manual transcription into each system.
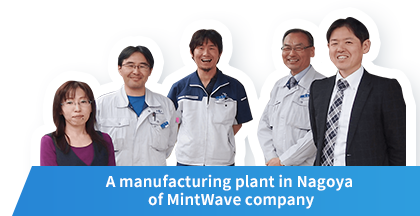
Previously, inventory management tasks took approximately 840 minutes per month. However, with the adoption of i-Reporter, the time-consuming tasks of handwriting on paper or manually calculating inventory quantities have been eliminated, and now the tasks can be completed with just a few taps on the screen. Subjectively, it feels like the working time has been reduced by about 90%.
achievements
Deployed by more than 4,000 companies!
No.1 share in paperless applications.
-
Contech Market Document Creating / Management Solution
Ranked #1 by companies with installed base and with 42.3% market share!
2021.05.18 Deloitte Tohmatsu MIC Research Institute "Contech Cloud Solution Market Actual Conditions and Outlook 2021 Edition"
-
The paperless reporting solution
for on-site workGained 48.4% of Japanese domestic market share!
References: As researched by Fuji Chimera Research Institute, Inc. in Feb. YEAR of ICT Revolution during the Covid-19 Pandemic
-
User-base Over
207,673 user are using
i-Reporter(As of Apr, 2025)
-
ConMas i-Reporter
Businesses who Trust i-Reporter Deployed in over 4,262 companies
(As of Apr, 2025)
How to get i-Reporter deployed in your business
Please consider adopting our product after seeing the product description and demo.
Please feel free to contact us for any inquiries.
-
-
Product Explanation Seminar
-
Operation Training
& Free Trial -
Contract signing
-
Service Start /
Support
Frequently Asked Questions
What types of system are available?
The system can be provided either as a cloud service or on-site product. Please select the option that best suits your needs. Feel free to contact CIMTOPS or your distributor for more information.
Is it possible to trial the system before implementation?
Up until the end of March 2022, up to 100 users will be able to use all functions free of charge for up to three months as part of the "Support for work style reform and telework" programme. The trial can be selected either via the cloud or on-site versions. For more information, go to the i-Reporter free trial page.
Do you offer training courses or how-to-use workshops?
There are many distributors in each country and they can provide the training courses and technical supports. For details, please contact CIMTOPS or your distributor.
Can it be integrated with our own existing business system and various other cloud services?
It is possible to integrate our product with various business systems and various cloud services using the API and ConMas Gateway for external system integration. For details, please contact CIMTOPS or your distributor.

About Us
CIMTOPS Corporation is a Japanese software maker with a proven track record for making software to help companies in the manufacturing industry move to digital solutions such as production control schedulers, process control systems, and on-site digital reporting software.
-
For individual order manufacturing
Production scheduler & Process management system
-
BOP (Bill of Process) tool
- Company name
- CIMTOPS Corporation.
- Established
- October 1, 1991
- President and CEO
- Takashi Mizuno
- Headquarters
-
Shin-Meguro Tokyu Building 10F, 2-25-2 Kami-Osaki,
Shinagawa-ku, Tokyo 141-0021, Japan
TEL: 03-5721-4610 /FAX: 03-3491-4610
- Other offices
- Chubu Area (Kariya) & Kansai Area (Kyoto)
- Overseas
- CIMTOPS (Shanghai) Information Technology Co. & CIMTOPS SG LAB Pte.
Our Customers
Deployed by more than 4,000 companies!
No.1 share in paperless applications.
Work such as warehousing,
inventory and picking can be made labour-saving and efficient.